TRUMPF customer C.HAFNER saves material with additive manufacturing // TruPrint 2000 saves up to 50 percent energy
TRUMPF 3D printers ensure cost-effective and sustainable series production
Ditzingen/Frankfurt, 31 October 2023 – With its 3D printers, the high-tech company TRUMPF reduces CO2 emissions compared to conventional manufacturing processes. Additively, the high-tech company and its customers manufacture series components cost-effectively. "We invest in climate protection out of conviction. This applies, for example, to the development of 3D printing solutions that contribute to environmentally friendly manufacturing. Our machines also pay off financially, if only because they are in the field for many years," says Amal Prashanth Charles, responsible for sustainability in 3D printing at TRUMPF. The high-tech company is presenting sustainably manufactured components at Formnext, the world's leading trade fair for 3D printing, in Frankfurt.
Customers manufacture environmentally friendly with 3D printers from TRUMPF
C.HAFNER relies on 3D printers from TRUMPF for sustainable component manufacturing. The company recycles secondary materials containing precious metals and processes the recovered platinum and gold into electrodes and watch cases, for example. "With 3D printers from TRUMPF, we save energy and material," says Jochen Heinrich, responsible for the development of powder applications at C.HAFNER. For example, the production of platinum-iridium electrodes using 3D printing emits 31 percent less CO2 compared to conventional manufacturing processes. The CO2 footprint of watch cases made of gold can be reduced by more than 50 percent through additive manufacturing. "This is possible because 3D printing allows us to manufacture very close to the final shape compared to conventional processes, requires less material for production and eliminates the need to build tools, " says Heinrich.
Environmentally friendly mass-produced parts from the 3D printer
"3D printing also makes TRUMPF's own series parts production more sustainable. One example is engine coolers for our lasers, where we have been able to reduce CO2 emissions per part produced by 83 percent compared to a conventionally produced version," says Charles. A 3D printer produces 47 engine coolers in a single print. The conventionally manufactured version consisted of several parts that had to be sourced and assembled individually.
TruPrint 2000 saves energy in every printing process
TRUMPF is presenting the new TruPrint 2000 at Formnext. Compared to the previous variant, the 3D printer has a larger building area . Users can thus print more parts in a single printing process. Energy consumption has remained the same despite the machine's increased productivity. "Printing dentures shows how great the energy-saving potential is: users can print more parts in half the time than before. This means that we have been able to reduce energy consumption per manufactured component by more than 50 percent," says Charles.
With the new TruPrint 2000 TRUMPF is also introducing a new gas filtration system that permit to save the filter housing, reducing drastically the components the customer needs to dispose when the filtering element needs to be changed.
Digital photographs in print-ready resolution are available to illustrate this press release. They may only be used for editorial purposes. Use is free of charge when credit is given as “Photo: TRUMPF”. Graphic editing – except for cropping out the main motif – is prohibited. Additional photos can be accessed at the TRUMPF Media Pool.
Contact person
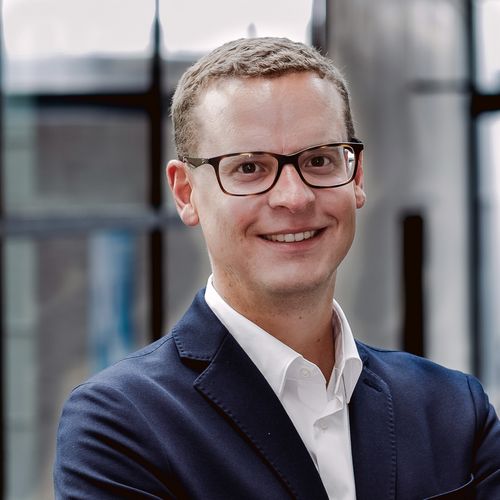