1. Extrémně těsné svařování
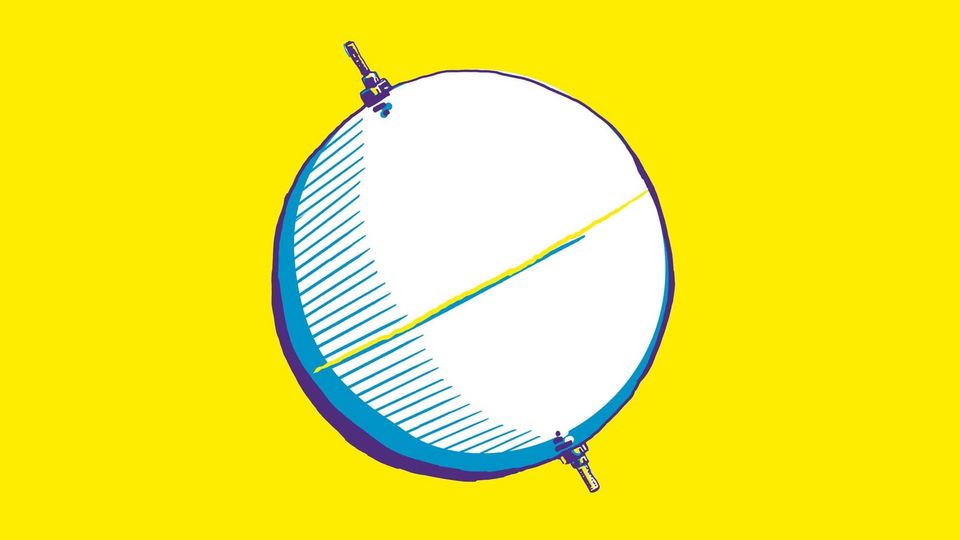
Těsně svařená kulová nádrž
Že lasery dokáží svařovat přesně a velmi spolehlivě těsně, se prokázalo teprve u kardiostimulátorů, později u E-autobaterií. Také v oblasti letů do vesmíru je nyní využíváno získané procesní know-how a je svařována nerezová ocel, hliník, titan a superslitiny jako Inconel. Hlavními důvody jsou vysoká rychlost postupu mnohdy několik metrů za minutu a čisté svary díky sensorem optimalizovanému působení energie. Těsné svařování laserem se stává standardem tam, kde to je zvláště důležité: u raketových nádrží. Když technici objeví, že nádrže propouštějí i jen nepatrné množství paliva, musí tým odložit start rakety. Pokud netěsnost nikdo neobjeví, dojde ke katastrofě při spuštění pohonných jednotek. Proto firmy působící v oblasti letů do vesmíru raději pomocí laseru dosahují co nejvyšší jistoty.
2. Spojování nestejných materiálů
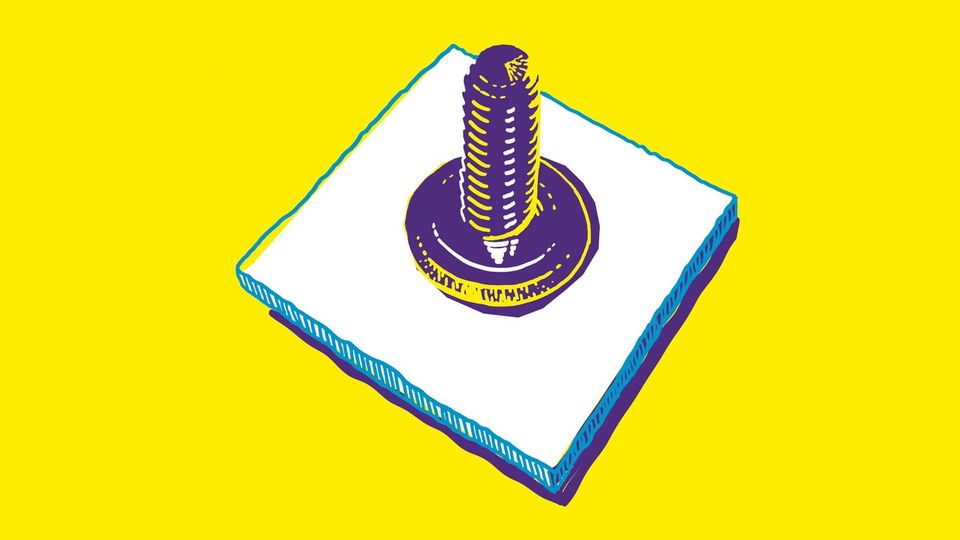
Přímé spojení plast - kov
Lasery s ultrakrátkými impulzy při svařování tak jemně dávkují energii, že také nestejné materiály spojují nezlomitelně a plynotěsně. Například sklo a kov. Tyto kombinace jsou zvláště zajímavé pro optické komponenty u satelitů a možná také pro okna u kosmických stanic. Skvělým argumentem pro toto spojování laserem je, že je přímé. To znamená, nepotřebuje žádné zdlouhavé šroubové spoje nebo lepidla málo odolná vůči teplotám – které rovněž navyšují hmotnost. NASA již přezkoušela s ultrakrátkými impulzy svařované spojení skla a invaru, speciální slitiny, a plánuje jeho používání. V mnoha případech je přímé spojování se sklem a jiným materiálem nebo spojení sklo - sklo vůbec jedinou možností použití skla ve vesmíru. Také přímé spojování pomocí laserů s krátkým pulzem u termoplastů vyztužených uhlíkovými vlákny a jiných plastů s kovem nahrazuje stále častěji klasické šroubové spoje.
3. Tištěné strukturované díly
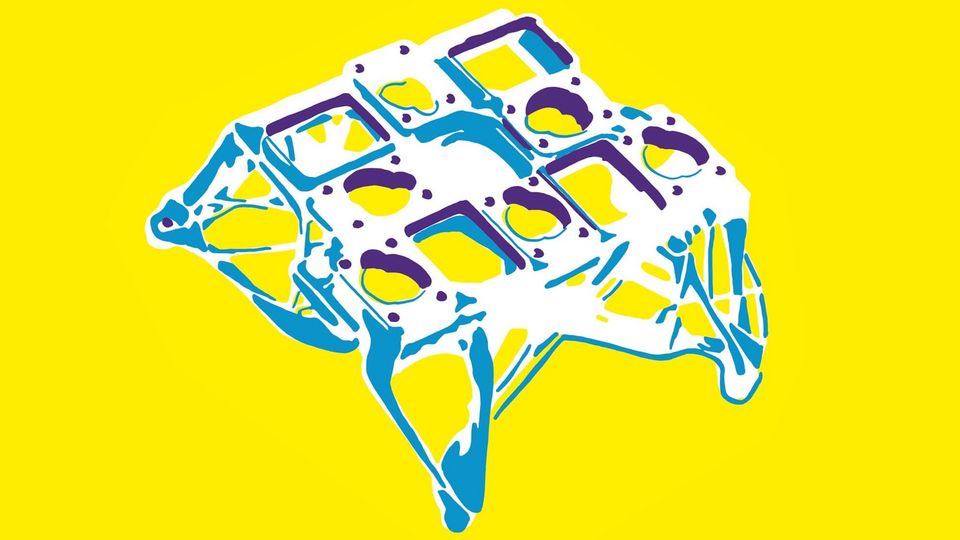
Držák kamery pro satelity
Díky každému kilogramu, který není potřeba, je levnější let do vesmíru. U raket, protože vynesou více užitečného zatížení, když váží méně. A také u užitečného zatížení samotného je příznivější, když váží méně. To bylo hlavní myšlenkou, když firmy začaly tisknout strukturované díly, jako jsou držáky kamer: Použít tak málo materiálu jak je možné a uspořádat ho čistě funkčně. Mezitím je také jasné, že designová revoluce činí díly nejenom lehčími, ale dokonce stabilnějšími, protože jsou možné lepší konstrukce. A nakonec: Výroba pomocí 3D tisku je –především u superslitin odolných vůči teplotám jako Inconel – nakonec podstatně výhodnější než klasický mechanický postup jako soustružení. V oblasti letů do vesmíru vedou vlastně všechny cesty k 3D tiskárně.
4. Satelitní komunikace
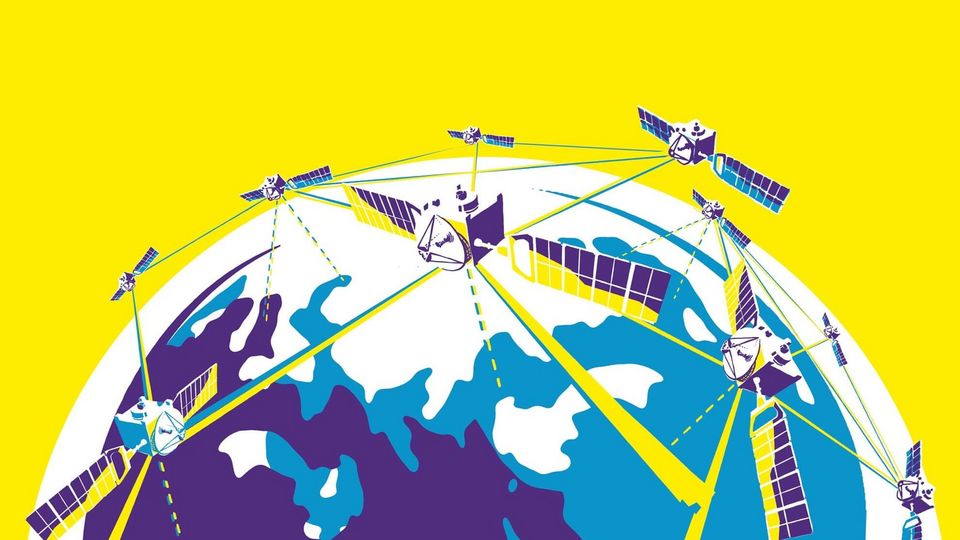
Přenos dat laserem
Přenos dat ve vesmíru bude brzy probíhat prostřednictvím laserových signálů. Nízko létající LEO satelity obíhají pouze s asi 7.8 kilometry za sekundu (!) kolem zeměkoule. Pro stabilní datové spojení tedy nestačí mít kontakt s LEO satelitem, neboť ten již brzy bude nad jiným kontinentem. Je potřeba síť. LEO satelity mají do budoucna komunikovat prostřednictvím laseru: laserový info-paprsek přeletí přes tisíce kilometrů. Také komunikace oběžná dráha - Země přejde brzy na lasery, protože lasery mají až stokrát vyšší přenosovou rychlost dat než rádiové vlny. Dobré zprávy, protože potřeba výměny dat razantně stoupá kvůli streamingu, UI-cloud-computingu, Internet of Things (internetu věcí) a mnoha dalším službám na bázi dat. Také užitečné: Laserem chráněný přenos dat je z fyzikálních důvodů bezpečný proti zachycení – pokus o špionáž byl okamžitě odhalen. Již dnes funguje laserový přenos satelit - satelit a satelit - Země u hightech armádních satelitů. Experti odhadují, že se technologie za deset let prosadí také u komerčních sítí.
5. Pohonné jednotky a thruster (pomocná raketa) aditivně vyráběné (také měď!)
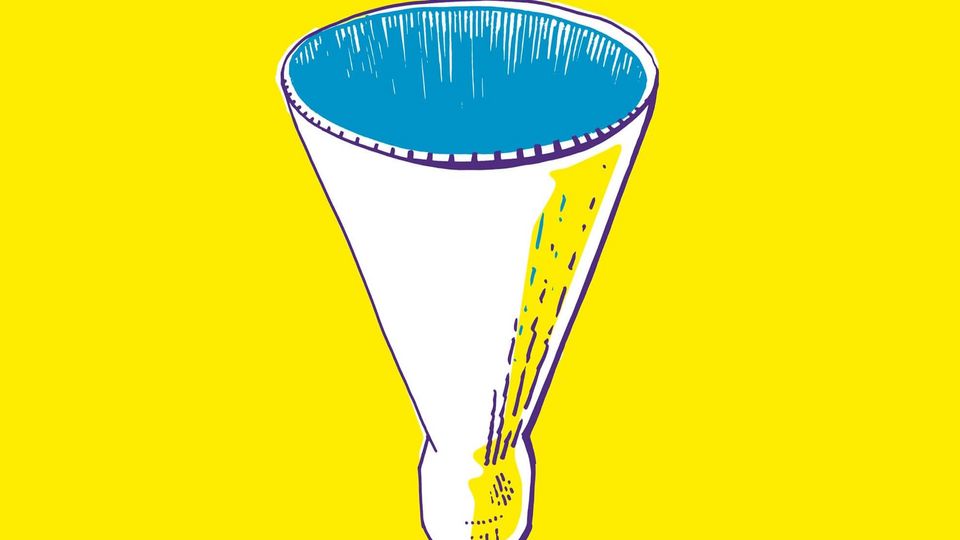
Bimetalická raketová tryska
Pohonné jednotky raket a thrustery - malé pohonné jednotky, které směrují, brzdí nebo zrychlují sondy nebo satelity – potřebují pro palivo uvnitř umístěné chladicí kanály, aby fungovaly. U mini-thrusterů není již kvůli malé tloušťce stěn možné nic jiného než aditivní výroba a také u větších není nic výhodnějšího. Pomocí laserového práškového navařování se podaří také větší struktury s kanály umístěnými uvnitř jako jsou třeba trysky pohonných jednotek. A navíc: Postup je vhodný pro bimetal a požadované kovy uspořádá podle funkce. V případě trysky například uvnitř umístěná měď pro optimální tepelný tok a vně umístěná silná vrstva Inconel pro stabilitu.