レーザーでは、鋼、アルミニウム、ステンレススチールや非鉄金属、そしてプラスチック、ガラス、木材やセラミックなどの非金属材料を含めて、産業用加工で普及しているあらゆる材料を、高い安全性と品質で切断することができます。このツールでは多種多様な板厚が切断可能であり、その範囲は0.5から30ミリメートル以上にまでわたります。このように極めて幅広い材料に対応可能であるため、レーザーは金属及び非金属領域での多数の用途でナンバー1の切断ツールです。
レーザ切断とは、様々な板厚を持つ金属/非金属素材の切断を可能にする切断プロセスのことを指しています。このプロセスの基礎として、レーザ光がガイドされ、形成され、集光されます。この光線が加工品に当たると、材料は強く加熱され、溶解又は蒸発します。ここでレーザー出力全体が集中する点は、多くの場合直径0.5 mm未満です。この箇所に、伝熱による流出可能量を超える熱が吸収されると、レーザー出力が材料に完全に浸透し、切断プロセスが開始したことになります。他の方法では強力なツールが巨大な力でシートに作用するのに対して、レーザー光線では加工作業が非接触で行われます。そのため、ツール自体が摩耗することも、加工品に変形や損傷が発生することもありません。
レーザーカッティングの利点
レーザーカッティングのプロセス
レーザーカッティングの基礎は、焦点に集光したレーザー光線と加工品の間での相互作用です。このプロセスが安全かつ正確に行われるように、多数のコンポーネントと補助具がレーザー光線の表面と周囲で使用されます。それらは以下の図で説明されています。
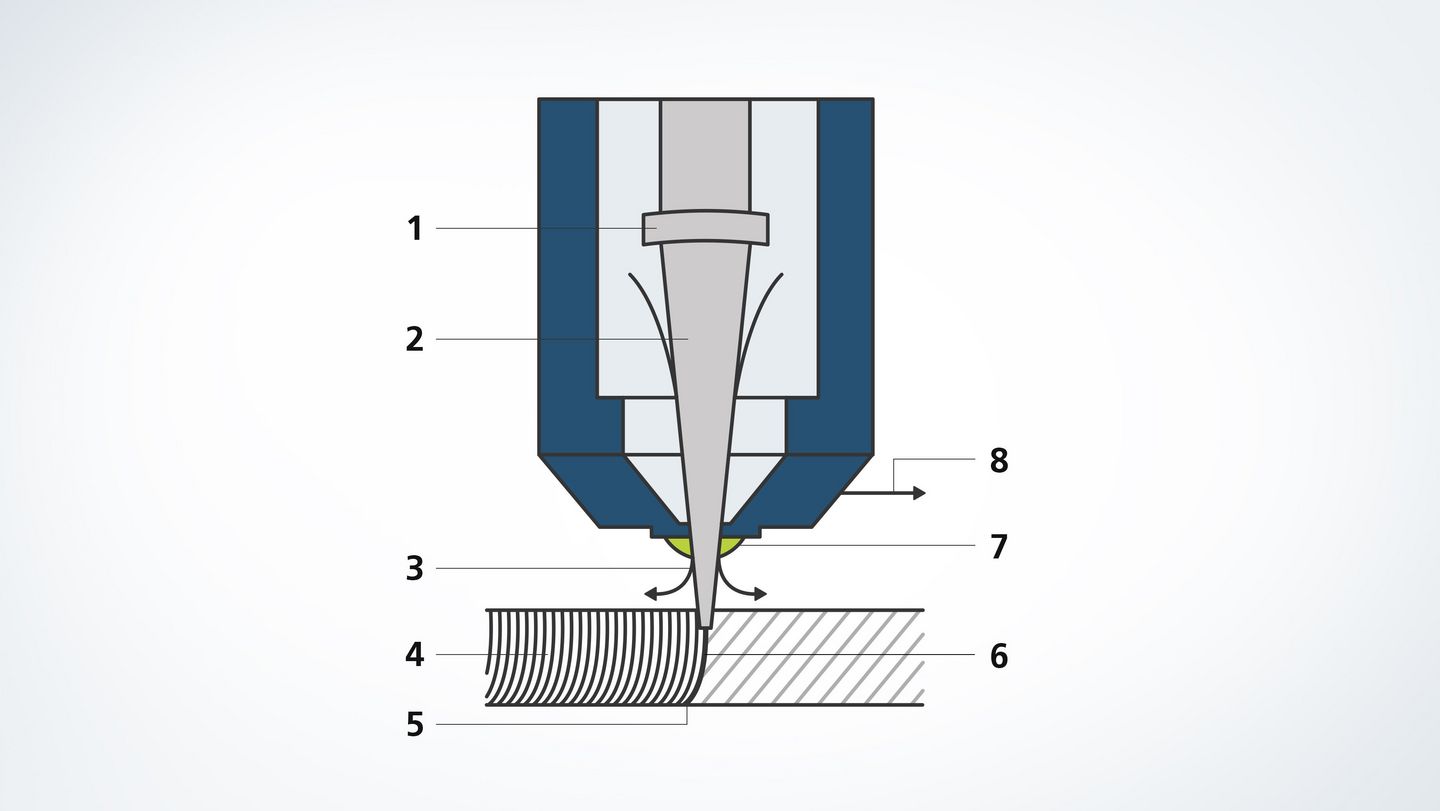
- 焦点合わせ光学ユニット: レンズ/ミラー光学系は、レーザー光線を加工箇所に収束します。
- レーザー光線: レーザー光線は、それが当たった加工品を溶解又は蒸発するまで加熱します。
- アシストガス: 発生した溶融物を、アシストガスを使用してカーフから吹き飛ばします。このガスは、レーザー光線と同軸方向にノズルから放出されます。
- 切断溝: レーザーカッティングでは、切断エッジに典型的な溝パターンが発生します。切断速度が低い場合、この溝はレーザー光線に対してほぼ平行に延びます。
- 溶融: 集光されたレーザー光であるレーザー光線がコンタに沿ってガイドされ、材料を局所的に溶融します。
- 加工品の切断面: カーフの幅は、収束されたレーザー光線の幅とほとんど変わりません。
- ノズル: レーザー光線とアシストガスは、切断ノズルを通じて加工品へ導かれます。
- 切断方向: カッティングヘッド又は加工品を特定の方向に動かすことで、カーフが発生します。
全レーザーカッティング方法の一覧
金属/非金属材料の切断において、汎用ツールであるレーザーは多くのケースで最適な手段です。レーザー光線はほぼあらゆるコンタを素早く自由自在に切断します。コンタの形状がいかに精緻で複雑であっても、材料がいかに薄くても問題ありません。その際、加工プロセスと結果はアシストガスの種類と圧力に左右されます。
レーザーカッティングプロセスに影響を及ぼすパラメータ
焦点距離は加工品でのパワー密度とカーフ形状に影響を及ぼします。焦点直径はカーフ幅の決定要因であり、焦点距離と同様にカーフ形状に影響を及ぼします。
材料が溶融し始める点である加工閾値を超えるには、単位面積当たりのエネルギーが一定値に達する必要があります。これは以下の公式で定義されています: 単位面積当たりのエネルギー = パワー密度 x 加工品への作用時間。
正しいノズルの選択はパーツ品質にとって極めて重要です。ノズルの直径によって、ガス流の形状とガス量の両方が定まるからです。
連続波モードとパルスモード: 運転モードを介してレーザーエネルギーを制御して、加工品に連続的又は断続的に到達させることができます。
切断速度は各切断作業と加工の対象となる材料に応じて決定されます。原則的には、利用可能なレーザー出力が高ければ高いほど、速く切断できると言えます。また、切断速度は板厚の増加に伴って低下します。それぞれの材料に対する速度設定が高すぎるか低すぎると、切断面粗さとバリ形成が増加します。
ほぼすべてのCO2レーザーは直線偏光レーザー光を発します。コンタを切断する際、切断結果は切断方向に伴って変化します。光が切断方向と並行に振動すると、エッジは滑らかになります。光が切断方向に対して垂直に振動するとバリが発生するため、直線偏光レーザー光は多くの場合、円偏光に変換されます。偏光度は目標となる円偏光にどれだけ到達しているかを示す指標であり、切断品質にとって決定的な意味を持ちます。固体レーザーでは切断結果が切断方向に左右されることがないため、偏光を変換する必要はありません。
切断方法に応じて様々なプロセスガスが使用され、異なる圧力でカーフに送り込まれます。例えばアルゴンと窒素はアシストガスとして、カーフ内の溶融金属と反応しないという利点を有しています。このガスは同時に、切断面を周囲から保護します。
高いレーザ出力と共に窒素と酸素のガス混合を使用すると、軟鋼やアルミニウムのバリを少なくすることができます。パーツ品質の向上は材質、材料合金、材料品質によって異なり、厚板では6~12ミリメートルの範囲となります。