- レーザー硬化では、炭素を含む鋼又は鋳鉄製加工品の表面を溶融温度ぎりぎりまで、原則的には約900から1400 ℃に加熱します。照射出力の約40 %が吸収されます。高温により、金属格子構造内の炭素原子の位置が変化します (オーステナイト化)。
- 指定温度に到達すると、レーザー光線は移動して、表面を送り方向に向かって継続的に加熱します。
- レーザー光線が先に移動次第、周囲の素材が高温層を極めて素早く冷却します。これは自己冷却と呼ばれます。急速に冷却されるため、金属格子構造は元の形に戻ることができず、マルテンサイトが形成されます。これにより、硬度が大幅に増します。
- 典型的な硬化層深さは0.1から1.5ミリメートルですが、材質によっては2.5ミリメートル以上になることもあります。

レーザ硬化
レーザー硬化は、高負荷を受ける複雑な部品の品質向上に最適です。入熱が特定の部分だけを狙って局所的に行われるため、加工時に発生する部品のひずみは皆無に等しくなります。非接触式のレーザー硬化法では、誘導加熱硬化や炎焼入れなどの従来の硬化法では実現不可能であるようなアプリケーションでさえも開発することができます。加工プロセスの精密制御が可能であるため、形状が複雑で精緻な部品も硬化することができます。その結果、機械的及び化学的負荷に対する耐性が強い表面が生み出され、とりわけ金型製造、自動車業界や農業機械に大きなメリットがもたらされます。
レーザー硬化の利点とは?
後処理の低減
入熱量が低いため、後処理作業が軽減されるか、不要になります。
小型で精緻な部品の硬化
レーザーでは別の方法と比較して、局所的な機能面であっても精密な硬化が可能です。
ひずみなし
従来の硬化法では入熱量が比較的高く、その後の冷却によりひずみが発生してしまうのに対して、レーザー硬化では部品がほぼ元の状態で維持されます。
正確な制御
レーザーテクノロジと温度調節により、入熱の精密制御が可能です。
短い加工所要時間と高い生産性
レーザーでは加工が非接触式にひずみなしで行われるため、加工所要時間が短縮され、前処理/後処理が発生する可能性が低下します。
どのような形状にも対応可能
TRUMPFのスキャン技術では部品上の硬化形状が素早く「オン・ザ・フライ」で変更可能であるため、光学ユニットもしくはシステム全体を改造する必要がありません。
レーザー硬化法の仕組み
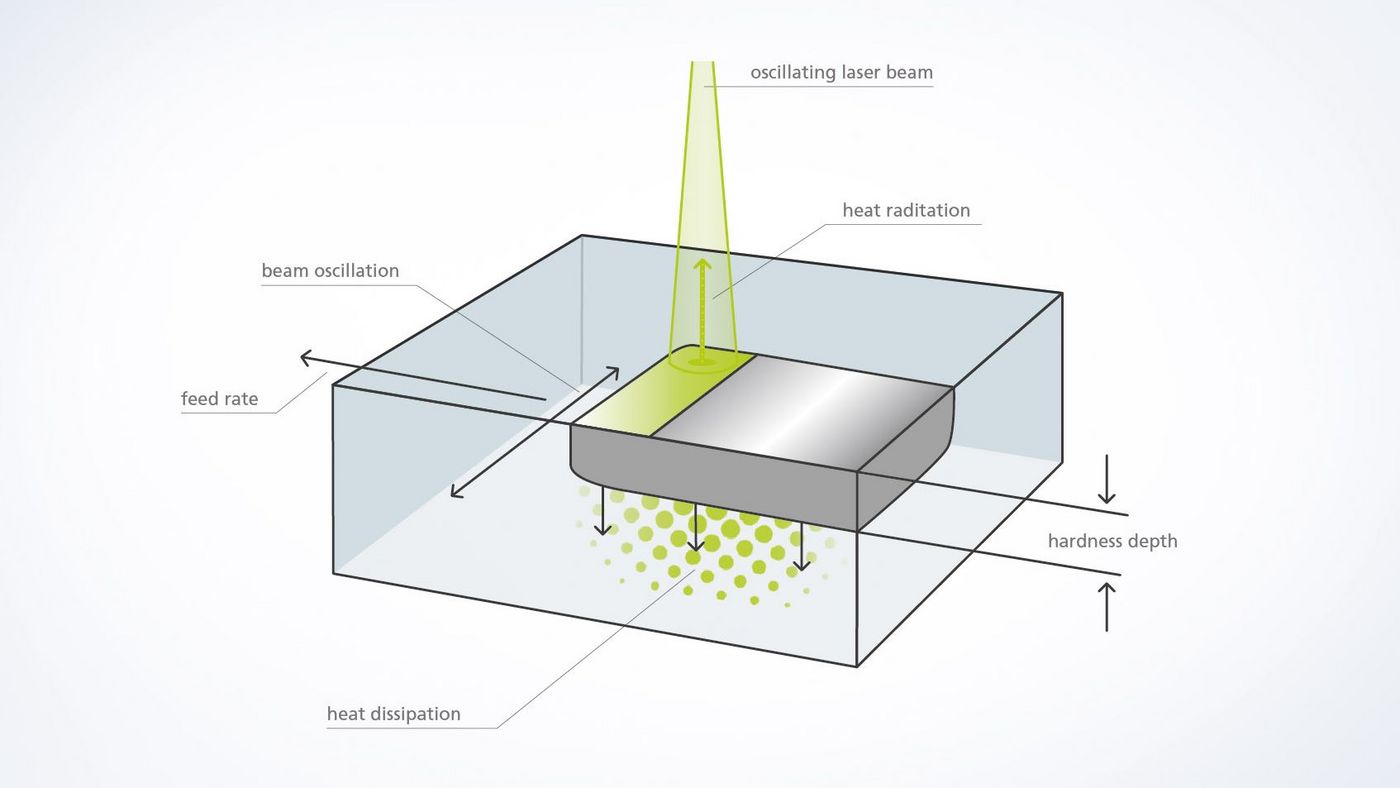
レーザー硬化に適した当社製品
ホワイトペーパー
問い合わせ