1. Soudage étanche extrême
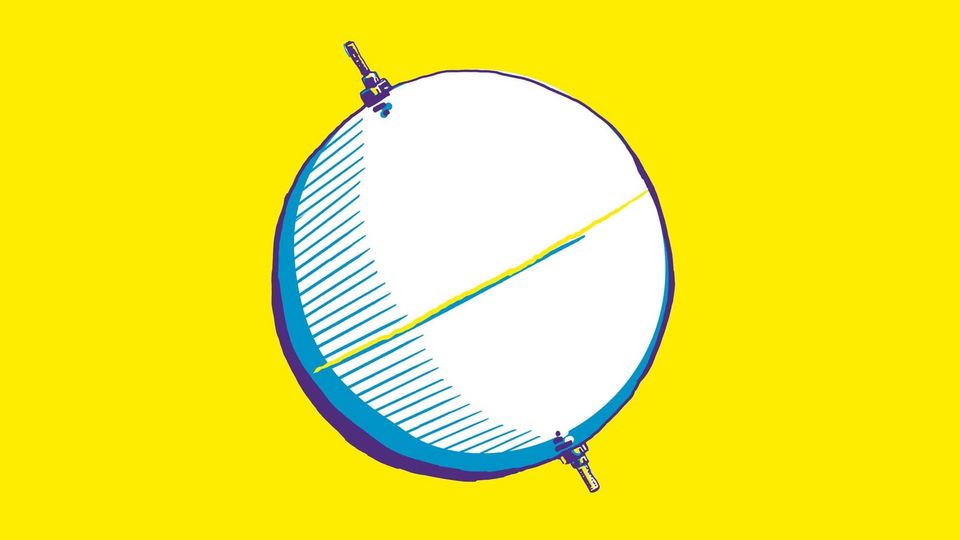
Réservoir sphérique à soudage étanche
C'est d'abord dans les stimulateurs cardiaques, puis dans les batteries pour voitures électriques, que le soudage étanche au laser a démontré son exactitude et son extrême fiabilité. L'astronautique tire désormais également parti de ce savoir-faire acquis en matière de processus pour souder de l'acier inoxydable, de l'aluminium, du titane et des superalliages comme l'Inconel. Les principaux atouts du procédé sont sa grande vitesse d'exécution, atteignant parfois plusieurs mètres par minute, et les soudures propres obtenues grâce à l'apport d'énergie optimisé par capteur. Le soudage étanche au laser se hisse au rang de standard là où il est particulièrement important : dans les réservoirs de fusée. La moindre fuite de carburant, aussi infime soit-elle, détectée par les techniciens au niveau d'un réservoir oblige l'équipe à annuler le départ de fusée. Si personne ne détecte la fuite, c'est la catastrophe lors du lancement des moteurs. C'est la raison pour laquelle les entreprises de l'astronautique préfèrent avoir recours au laser pour limiter aux maximum les risques.
2. Assemblages hétérogènes
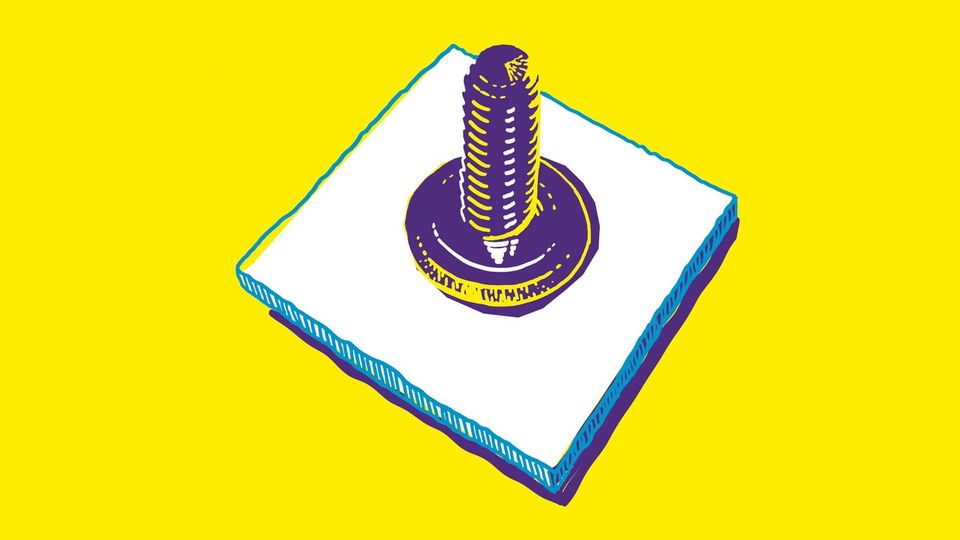
Assemblage direct plastique-métal
Les lasers à impulsions ultracourtes permettent un dosage d'énergie si fin lors du soudage qu'il est possible d'obtenir un assemblage incassable et étanche au gaz même avec des matériaux différents, comme le verre et le métal. Ces combinaisons sont particulièrement intéressantes pour les composants optiques des satellites et potentiellement aussi pour les fenêtres des stations spatiales. L'atout majeur de cet assemblage laser est qu'il est direct. Il n'y a donc pas d'assemblage compliqué par vis ni d'ajout de colles sensibles à la température, ce qui augmenterait en outre le poids dans les deux cas. La NASA a d'ores et déjà étudié un assemblage soudé par impulsions ultracourtes de verre et d'Invar, un alliage spécial, et prévoit de l'utiliser. Dans de nombreux cas, les assemblages directs de verre avec un autre matériau ou les assemblages verre-verre sont les seules solutions qui permettent l'utilisation du verre dans l'espace. Les assemblages directs au laser à impulsion courte de thermoplastiques renforcés de fibres de carbone et d'autres matières plastiques avec du métal remplacent également de plus en plus les assemblages par vis classiques.
3. Impression de composants structurels
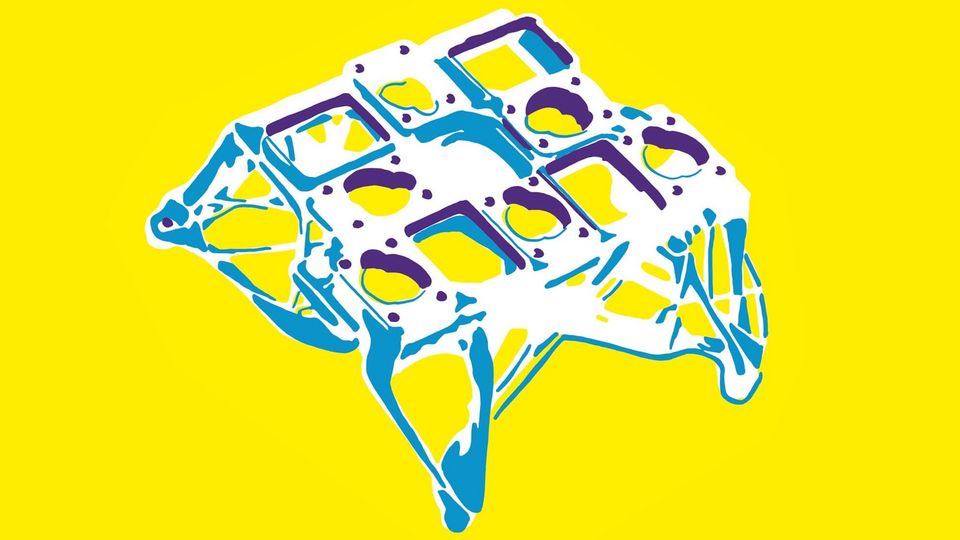
Support de caméra pour satellites
Chaque kilo en moins rend le vol dans l'espace plus rentable. Des fusées plus légères peuvent en effet transporter une plus grande charge utile. Le vol coûte aussi moins cher lorsque la charge utile elle-même est plus légère. C'est l'idée principale qui a poussé les entreprises à commencer à imprimer les composants structurels, comme les supports de caméra : utiliser le moins de matériau possible et ne pas sortir du cadre de la pure fonctionnalité. Il est maintenant évident que la révolution en matière de design ne fait pas qu'alléger les composants mais les rend aussi plus stables car de meilleures constructions sont possibles. Enfin, la fabrication additive est au bout du compte nettement moins coûteuse que les procédés mécaniques classiques comme le tournage, en particulier pour les superalliages résistants aux températures extrêmes comme l'Inconel. En somme, dans l'astronautique, presque tous les chemins mènent à l'imprimante 3D.
4. Communication par satellite
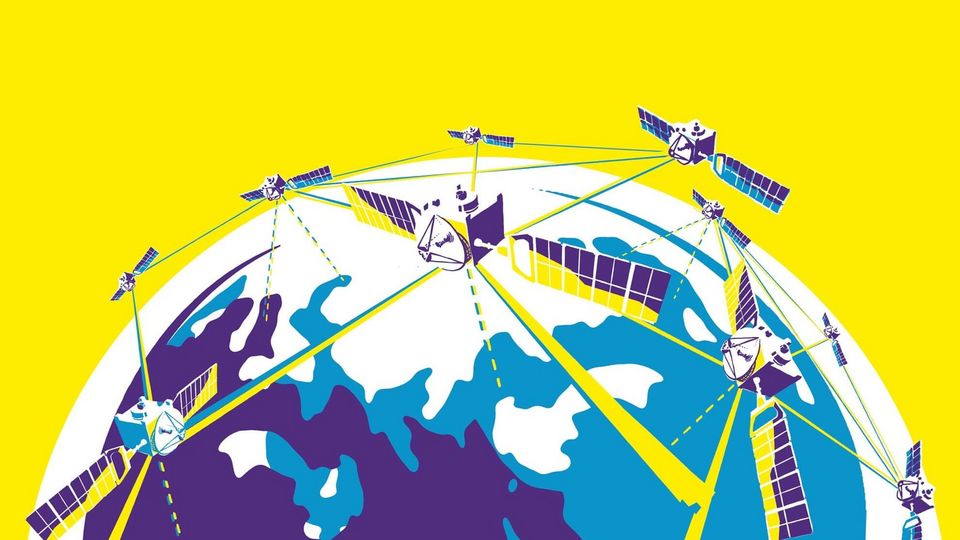
Transmission de données laser
La transmission de données dans l'espace fonctionnera bientôt par le biais de signaux laser. Les satellites en orbite basse (LEO) tournent à une vitesse d'environ 7,8 kilomètres par seconde (!) autour de la Terre. Pour une connexion de données stable, disposer d'une liaison avec un seul satellite LEO n'est donc pas suffisant puisque celui-ci survole déjà un autre continent. C'est le réseau qui fait la différence. A l'avenir, les satellites LEO communiqueront par laser : via un rayon d'information laser volant sur des milliers de kilomètres. L'échange orbite-Terre passera lui aussi bientôt au laser car les lasers ont une vitesse de transmission de données jusqu'à cent fois plus élevée que celle des ondes radio. De bonnes nouvelles, car les besoins en matière d'échange de données augmentent à vitesse grand V avec le streaming, l'informatique dématérialisée basée sur l'IA, l'Internet des objets et de nombreux autres services basés sur les données. Un autre avantage physique de la transmission de données laser est qu'elle ne peut pas être interceptée : une tentative d'espionnage serait immédiatement détectée. La transmission laser satellite-satellite et satellite-Terre est déjà utilisée aujourd'hui pour les satellites militaires de haute technologie. Les spécialistes estiment que cette technologie s'imposera également dans les réseaux commerciaux d'ici dix ans.
5. Fabrication additive de moteurs et de propulseurs (cuivre inclus !)
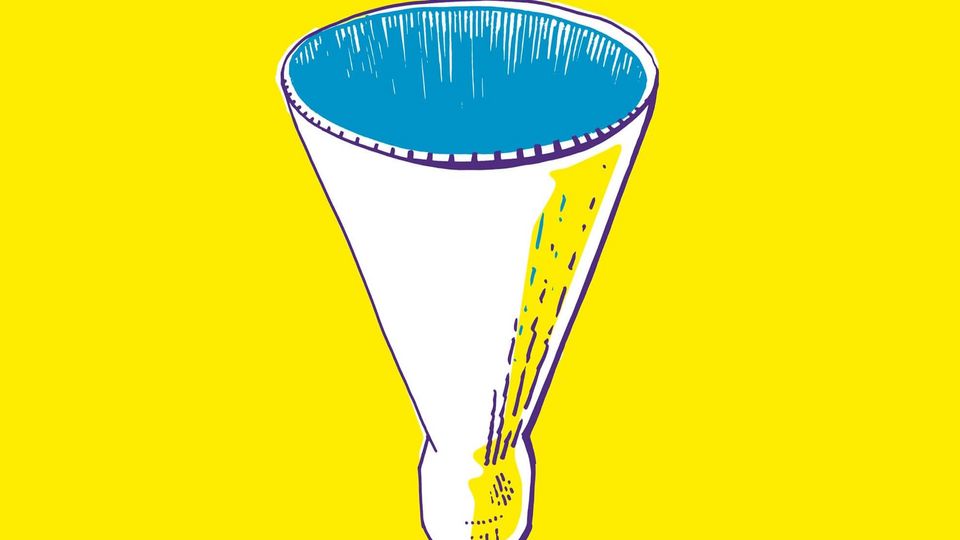
Tuyère de fusée bimétallique
Pour fonctionner, les moteurs-fusées et les propulseurs, de petits moteurs servant à orienter, freiner ou accélérer les sondes et les satellites, nécessitent des canaux de refroidissement internes pour le carburant. La fabrication additive est la seule solution possible pour les mini-propulseurs du simple fait de leur faible épaisseur de paroi. Quant aux propulseurs de plus grandes dimensions, elle reste la solution la moins chère. Le rechargement par dépôt laser permet aussi d'obtenir de plus grandes structures avec canaux internes comme les tuyères de moteur. Atout supplémentaire : le procédé prend en charge la fabrication de composants bimétalliques et assemble les métaux souhaités selon leur fonction. Dans le cas de la tuyère, par exemple, il s'agit de cuivre à l'intérieur pour un flux thermique optimal et d'une solide couche d'Inconel à l'extérieur pour la stabilité.