Todos los materiales habituales del mecanizado industrial (desde acero, aluminio, acero inoxidable o chapas metálicas, hasta materiales no metálicos como plásticos, vidrio, madera o cerámica) se pueden cortar con láser de forma segura y con gran calidad. Con el útil se pueden cortar espesores de chapa muy variados, desde 0,5 hasta más de 30 milímetros. Este espectro de materiales tan amplio hace que el láser sea el útil de corte número 1 para múltiples aplicaciones en el ámbito metálico y no metálico.
El corte con láser como procedimiento de corte sin contacto
El corte por láser se refiere a un procedimiento de separación con el que se pueden cortar materiales metálicos y no metálicos de distintos espesores. Se basa en un rayo láser que se guía, se conforma y se concentra. Cuando este incide en la pieza, el material se calienta tanto que se funde o se evapora. Toda la potencia del láser se concentra en un punto cuyo diámetro suele ser menor de medio milímetro. Si en este punto se concentra más calor del que se puede evacuar mediante la conducción de calor, el rayo láser atraviesa el material completamente, así comienza el proceso de corte. Mientras que con otros procedimientos la chapa recibe el efecto de útiles enormes con grandes fuerzas, el rayo láser lleva a cabo su trabajo sin contacto alguno. Así, ni se desgasta el útil, ni aparecen deformaciones o daños en la pieza de trabajo.
Las ventajas del corte con láser
El proceso del corte con láser
El corte por láser está basado en la interacción entre un rayo láser enfocado y la pieza de trabajo. Para que este proceso se lleve a cabo de forma segura y precisa, entran en juego multitud de componentes y medios auxiliares en el rayo láser y en su entorno que se aclaran en el siguiente gráfico.
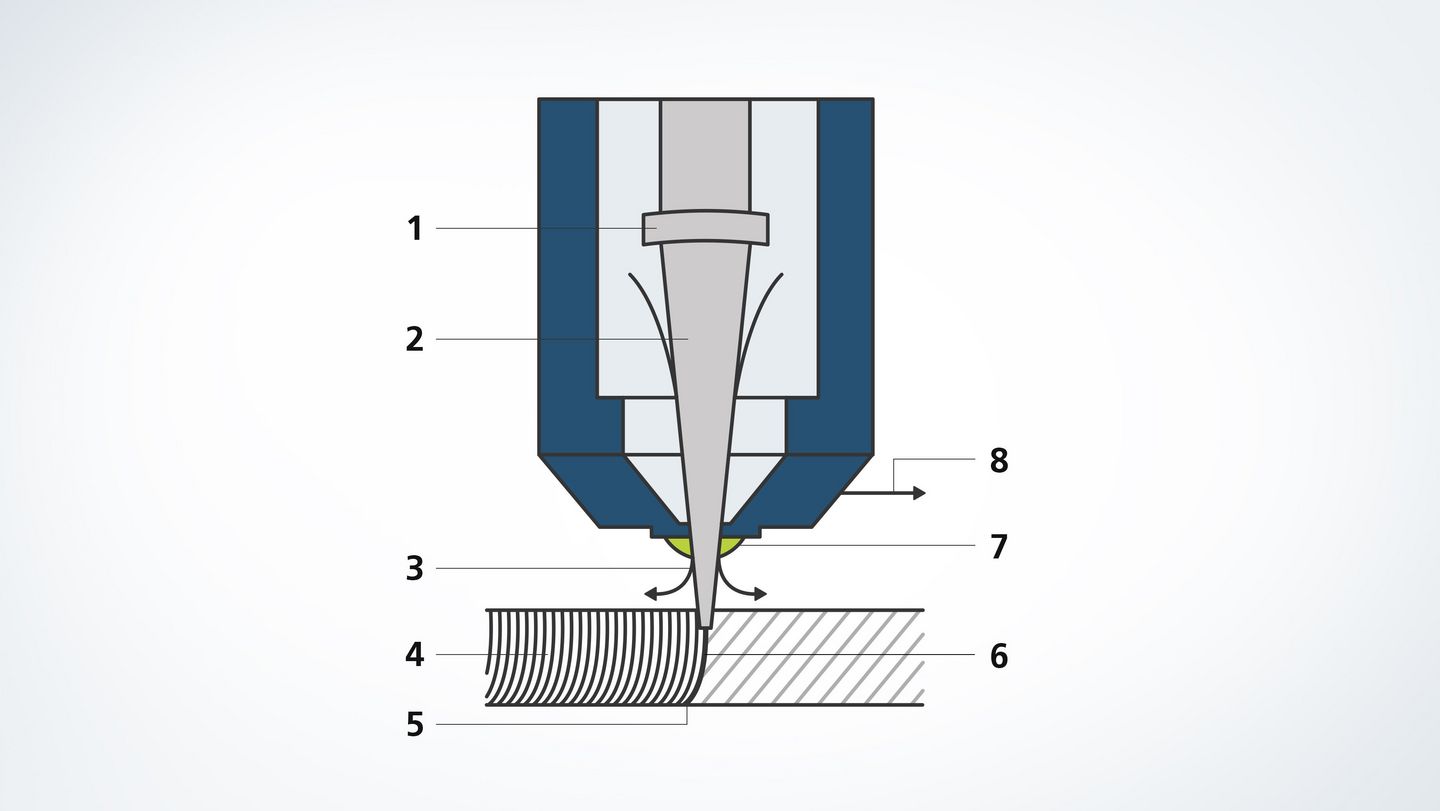
- Óptica de enfoque: las ópticas de espejo y de lentes enfocan el rayo láser sobre el punto de mecanizado.
- Rayo láser: el rayo láser incide en la pieza y la calienta hasta que se funde o se evapora.
- Gas de corte: con ayuda del gas de corte, la colada que se crea se retira de la ranura de corte mediante soplado. El gas de corte sale de la tobera coaxialmente al mismo tiempo que el rayo láser.
- Estrías de corte: en el corte por láser, el borde de corte recibe un patrón de estrías característico. Con una velocidad de corte reducida, estas estrías discurren prácticamente en paralelo al rayo láser.
- Colada: el rayo láser (luz de láser concentrada) se guía a lo largo del contorno y funde el material localmente.
- Frontal de corte: en la pieza de corte, la anchura de la ranura de corte apenas supera la del rayo láser enfocado.
- Tobera: el rayo láser y el gas de corte inciden sobre la pieza a través de la tobera de corte.
- Dirección de corte: mediante el movimiento del cabezal de corte o de la pieza en una dirección determinada, se produce la ranura de corte.
Las múltiples aplicaciones del corte por láser
Todos los procesos de corte por láser de un vistazo
Cuando se trata del corte de materiales metálicos y no metálicos, el láser es la primera elección en muchos casos como útil universal. El rayo láser puede cortar prácticamente cualquier contorno con rapidez y flexibilidad, ya sea una forma intrincada y complicada, o los materiales extremadamente delgados. Los distintos gases y presiones de corte influyen en el proceso de mecanizado y en el resultado.
Parámetros que influyen en el procedimiento de corte por láser
La posición del foco influye en la intensidad de la radiación y en la forma de la ranura de corte en la pieza de trabajo. El diámetro del foco determina el ancho de la ranura y también la forma de la ranura de corte.
Para que se supere el umbral de mecanizado (es decir, el punto en el que el material comienza a fundirse) se necesita una energía determinada por superficie. Esta se define como: energía por superficie = intensidad de la radiación x tiempo de aplicación sobre la pieza de trabajo.
La selección de la tobera adecuada es determinante para la calidad de las piezas. Así, el diámetro de la boquilla determina tanto la forma del chorro de gas como la cantidad de gas.
Funcionamiento de onda continua o pulsaciones: mediante el modo de funcionamiento se puede controlar si la energía del láser se proyecta sobre la pieza de forma continua o con intervalos.
En función de cada tarea de corte y del material que se ha de mecanizar, se establece la velocidad de corte. En general, cuanto mayor sea la potencia láser disponible, más rápidamente se podrá cortar. Además, la velocidad de corte desciende al aumentar el espesor del material. Si la velocidad está ajustada demasiado alta o demasiado baja para el material correspondiente, esto causa una mayor rugosidad y formación de rebabas.
Casi todos los láseres de CO2 emiten luz láser con polarización lineal. Si se cortan contornos, el resultado del corte cambia con la dirección del corte: si la luz oscila en paralelo a la dirección de corte, el borde será liso. Si la luz oscila en perpendicular a la dirección de corte, se generará rebaba. Por tanto, la luz láser con polarización lineal se transforma generalmente a una polarización circular. El grado de polarización indica hasta qué punto se ha alcanzado la polarización circular que se pretende y es decisivo para la calidad del corte. En los láseres de estado sólido, la polarización no debe modificarse, estos proporcionan resultados de corte independientes de la dirección.
En función del proceso de corte, se emplean distintos gases de proceso que se impulsan a través de la ranura de corte con distintas presiones. Cuando se usan como gas de corte el argón y el nitrógeno, por ejemplo, tienen la ventaja de que no reaccionan con el metal fundido en la ranura de corte. Al mismo tiempo, protegen la superficie de corte del entorno.
En combinación con una alta potencia láser, el uso de una mezcla de gas de nitrógeno y oxígeno puede conducir a la reducción de las rebabas en el acero de construcción y el aluminio. La mejora de la calidad de la pieza depende del tipo, la aleación y la calidad del material en los rangos de chapa gruesa entre seis y doce milímetros.