In tool construction and mold making or even for vehicle identification numbers, laser engravings with greater depths up to the millimeter range must be applied. In order to achieve the required depth, multiple processing steps must often be carried out in layers.

What is laser engraving?
During laser engraving, the laser beam removes material, creating a depression with different surface structures – the so-called laser engraving. Many materials can be engraved using a laser. When laser engraving metals, for example, rough structures are created which appear to be black, and smooth structures which seem to be white.
Laser engravings are often used in the automobile industry or in electromechanics. But laser engraving is also often implemented to create markings and deep engravings in rapid prototyping and rapid tooling.
How is the laser engraving production process carried out?
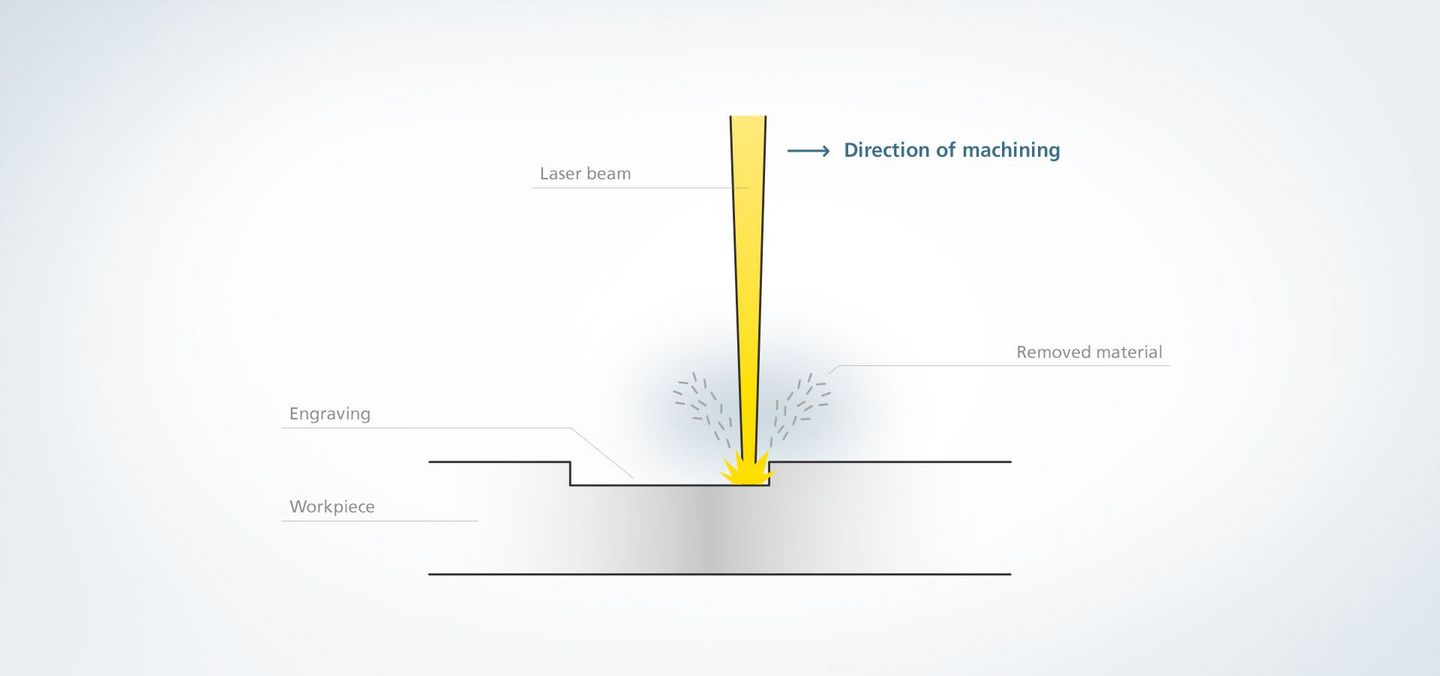
During laser engraving, the marking is applied thanks to a combined melt and evaporation ablation process. The irradiance of the laser beam is so high that the material melts and partially evaporates during processing. A depression is created in the material, the laser engraving. A typical engraving depth is 10 to 50 μm. The melt on the edge is driven out by the vapor pressure of the evaporating material and solidifies as melt rim as it cools. The engraving is U-shaped and becomes narrower the deeper the laser cuts into the material as the melt cannot be driven out completely. The heat input is greatly restricted - locally by the small laser spot and by the extremely short pulses in terms of time.
These are the procedures most often used for laser engraving
The top reasons for laser engraving
The laser as a non-contact and precise tool has a variety of benefits during ablation and therefore when engraving a material. Thanks to pulse frequencies and pulse durations which can be selected flexibly, each laser engraving can be adjusted individually to each material and according to any desired quality.
Despite the greater penetration depth into the material, laser engraving is faster than annealing due to the high repetition rates and resulting shorter cycle times.
The marking is extremely resistant to external factors thanks to the depression in the material created by laser engraving.
Thanks to locally restricted heat input, even temperature-sensitive sensors or electronic chips, for example, can be marked.
As the laser power can be specifically controlled, the marking results can always be repeated with precision.