Productive high-end machine
The TruPunch 5000 sets new standards for productivity, process reliability, and flexibility. Backlash-free drives enable the highest axis acceleration, and the high rotation speed of the C axis enables extremely fast tapping, as well as the productive processing of complex contours. Due to the powerful hydraulic drive you can punch with up to 1,600 strokes per minute and mark parts with 2,800 strokes per minute. Intelligent automation components and smart functions increase your productivity and process reliability.
Punch quickly and mark parts with 2,800 strokes/min: The TruPunch 5000 sets new standards for productivity.
The active die ensures low-scratch parts.
From material handling to tool automation – the machine will do everything for you.
The ToolMaster Linear for up to 90 tools guarantees a fast tool change.
Retractable clamps ensure the highest part quality and precision.

Scratch-free surfaces with size 5 tools
Regardless of whether you are producing extrusions or louvers, you can process sheets with flexibility using size 5 tools and the active die. For this component, the following tools were used among others: size 5 extrusion tool (active die), size 5 louver tool (active die), size 5 card guide tool, and roller offsetting tool.
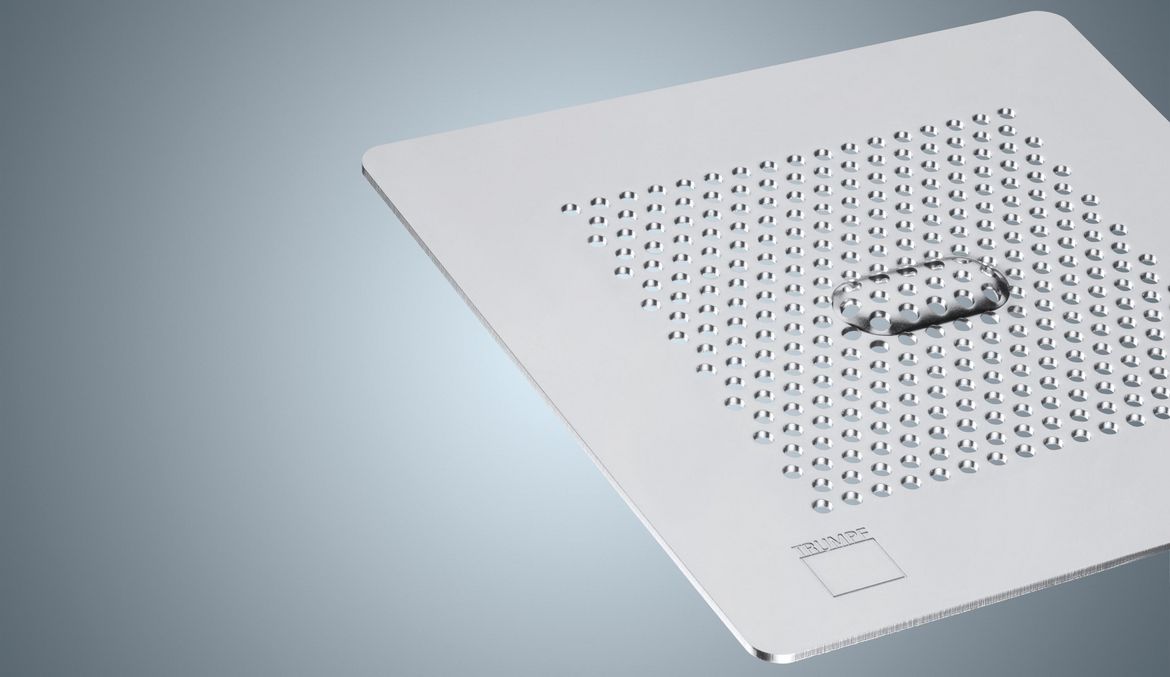
Integrated flattening
The "integrated flattening" machine function and the corresponding tool make it possible to even out surface irregularities during the punching process itself – without any post-processing.
TruPunch 5000 large format
|
TruPunch 5000 medium format
|
|
---|---|---|
Dimensions | ||
Width | 7610 mm 1 | 6540 mm 1 |
Depth | 8171 mm 1 | 7395 mm 1 |
Height | 2072 mm 1 | 2072 mm 1 |
Maximum stroke rate | ||
Punching (E = 1 mm) | 1350 1/min | 1600 1/min |
Marking | 3000 1/min | 3000 1/min |
Working range | ||
Punching mode, X axis | 3050 mm | 2500 mm |
Punching mode, Y axis | 1550 mm | 1250 mm |
Maximum sheet thickness | 8 mm | 8 mm |
Maximum workpiece weight | 280 kg | 200 kg |
Maximum punching force | 220 kN | 220 kN |
Tools | ||
MultiTool tool changing time | 0.3 s | 0.3 s |
Number of tools/clamps | 21 pieces / 4 pieces | 18 pieces / 3 pieces |
Part removal | ||
Maximum part size, part removal flap, punching | 500 mm x 500 mm | 500 mm x 500 mm |
Maximum part size, fixed chute, punching (with moving table) | 80 mm x 50 mm | 80 mm x 50 mm |
Consumption values | ||
Average power input of active auto-shutdown | 0.5 kW | 0.5 kW |
Average power input in production | 9.5 kW | 9.5 kW |
The technical data of all product versions as a download.
High productivity and the best quality: The innovative functions of the TruPunch 5000 guarantee the best processing results.
Quality

Ball tables or brush tables are available for gentle material handling.

The descending die enables scratch-free punching and forming processes and prevents the risk of things getting caught.
During the punching of sheet metal, compression and tensile stresses are placed on the workpiece which can cause sheet deformation. The "integrated flattening" machine function, and the corresponding tool, make it possible to even out surface irregularities during the punching process itself.

The repositioning cylinder clamps the sheet while the clamps open for repositioning.
Efficiency
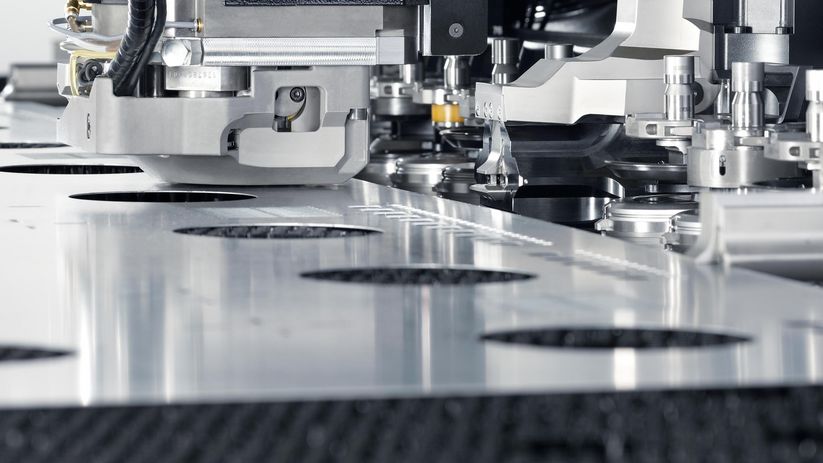
You can work efficiently using the retractable clamps: They facilitate processing even in the clamp dead area.
TRUMPF is the first manufacturer worldwide to offer punching machines that feature skeleton-free processing. This innovation saves material and increases process safety.
Process reliability
Before the tool change, smart punch monitoring checks whether a hole was actually punched into the sheet. In this way, the machine detects at an early stage when punches are broken, and can pass this information on to the operator.
Following the loading operation, the sheet format recognition function automatically compares the actual and target formats, thereby increasing process reliability.
Smart load supports sheet alignment on the machine. A sensor in the clamps detects when they do not grip the sheet correctly. If this is the case, the machine table, including sheet, moves.
If a finished part does not fall through the part removal flap as expected, a sensor detects this and the error can be rectified quickly.

Seamless integration of multiple TRUMPF machines into your own software environment is very easy. We have the right solution for every combination, whether it be integration into Oseon or a connection to monitoring and analysis tools. A connection to third-party software systems is also possible with our interfaces based on the OPC UA standard.

TruTops Boost
Construct and program your laser, punching, and combination punch laser machines intelligently with TruTops Boost, your all-in-one 3D solution. Numerous automated processes save you time-consuming routine processes and the joint nesting pool saves time and material. You also always have an overview of all manufacturing orders and order-based work.

Software
The software portfolio from TRUMPF optimizes your entire production process – from the customer query through to delivery of the finished part. TRUMPF combines the software intelligently with machines and services to create customized Industry 4.0 solutions for your Smart Factory.

Deburr geometries of different sizes directly on the machine. As such, you benefit from perfectly deburred workpieces and shorter production times.

As a result of the special tool design, with the size 5 cup tool for the active die, you can achieve form sizes that were previously not possible. In just one stroke, a diameter of 2.2 in. and a forming height of 0.4 in. are easily possible.

Save time by marking parts on the machine from below. The plastic ball roller of the punch gently counters the sheet, meaning there are no imprints or scratches.

TRUMPF offers the world's largest range of punching tools on the market. You will find the perfect solution for every punching and forming application.
You can choose automation options for your TruPunch 5000 and expand it step-by-step. You benefit from increased machine utilization, a fast tool change, and increased process reliability in automated multiple-shift operation.

Loading, unloading, and sorting
The SheetMaster guarantees fast and process-reliable loading, unloading, unstacking, and sorting.

Sorting
Various automation solutions sort your parts for you. Discover, for example, the SortMaster Box or the SortMaster Box Linear.

Disposal
Become acquainted with solutions for the disposal of scrap skeletons and punching slugs.

Tool handling
The tool automation system ToolMaster Linear guarantees fast tool changes.
This product range and information may vary depending on the country. Subject to changes to technology, equipment, price, and range of accessories. Please get in touch with your local contact person to find out whether the product is available in your country.
Footnotes-
The dimensions are approximate; the dimensions specified in the installation plan are valid.