From casting to milling to 3D printing: the history of the development of metal processing is also reflected in dental technology. Metal dental dentures, created with the casting technique, are now made using 3D printers. The procedure is even quicker and more affordable than when using milling technology. The dental industry has different metal 3D printing solutions for the additive manufacturing of dentures at its disposal. Using powder, the laser creates new workpieces layer by layer using the laser metal fusion technique (LMF). This procedure, also called selective laser melting (SLM) or powder bed fusion (PBD), is used in the highly precise manufacturing of implant-supported dental prostheses, for example. All in all, it is easy to implement a variety of individual geometries. Separation between pontics is eliminated, a milling radius correction is no longer necessary. The advantage: more space in important areas. Furthermore, retentions for plastic veneers and undercuts can be created effortlessly.
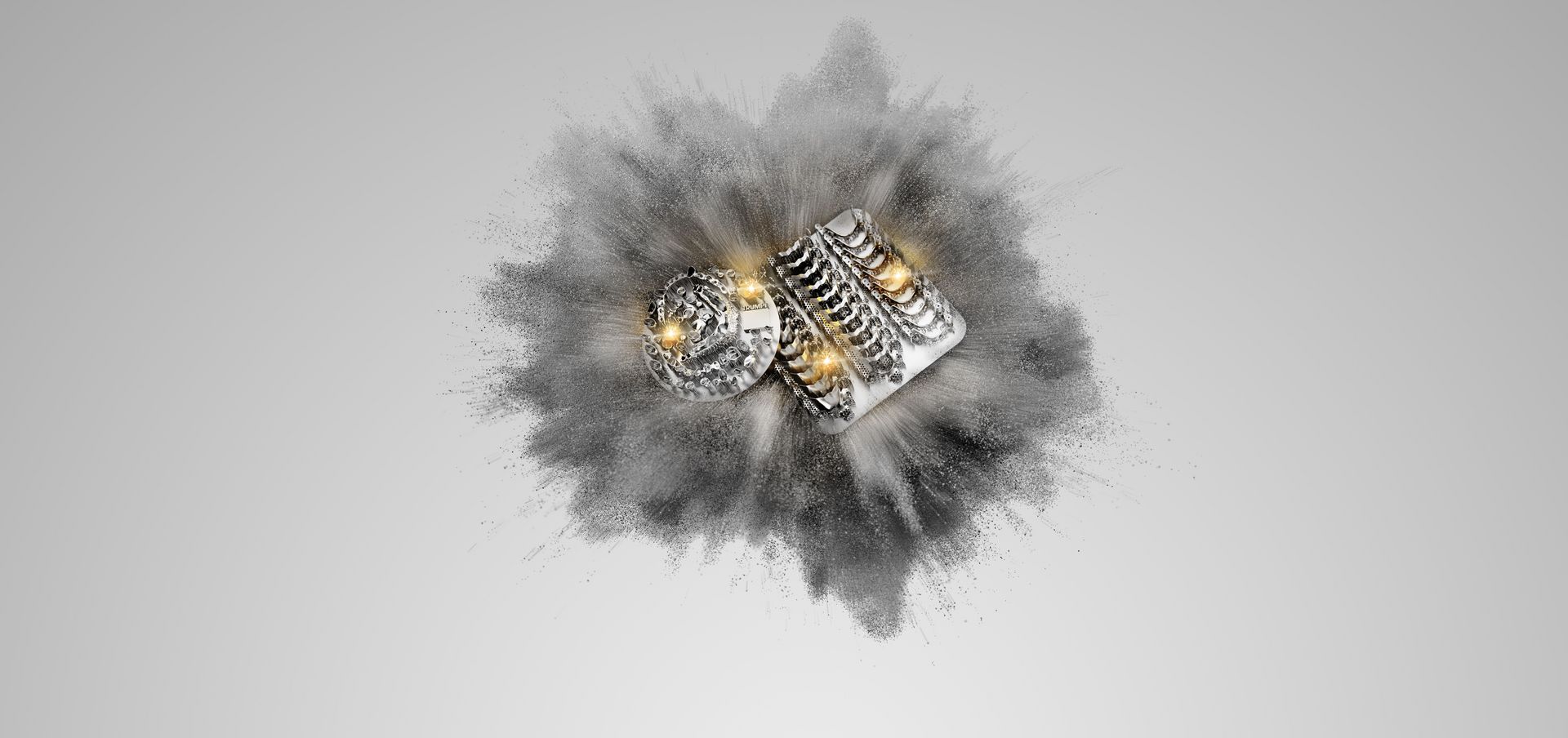
3D printing in dental technology
The production of implant-supported dental prostheses is the fastest growing segment in the dental industry all over the world. This is why it is becoming more and more important for dental laboratories to tap into this lucrative pioneering field, using highly productive 3D printers in response to the growing pressures of cost and competition in the industry. These pages will give you an overview of the advantages and benefits of metal 3D printers for your future business. You will also find out exactly which 3D printers, software solutions and services will provide you with the ideal set-up.
What is metal 3D dental printing and which procedures are available?
What are the advantages of metal 3D printing in dental technology?
Faster, more affordable and new dental indications thanks to a hybrid process chain. The investment in additive manufacturing is worthwhile for dental laboratories in many respects.
Many individual geometries can be implemented easily and productively with powder-based laser metal fusion (LMF). Functions such as Multilaser or Multiplate ensure efficient production of customized dental components.
A dental 3D printer produces dental prostheses much more quickly than conventional methods such as milling technologies. But metal 3D printers do not just benefit production, preparation is also much quicker thanks to the digital process chain. This means that dental technicians can work with digital data records transmitted to dental laboratories in real time. Thanks to digital molding, there are no plaster casts or silicone imprints.
With dental 3D printing, you can produce a large number of dental indications precisely, saving materials at the same time. Thanks to the digital connection of the TruPrint systems with milling machines, indications such as implant-supported crowns and bridges, telescopic crowns and secondary parts can be produced economically within a hybrid procedure. In this case, we truly see the benefits of direct printing of individual single abutments on special base parts (preforms) made of titanium or cobalt-chromium.
As the 3D printer only processes as much metal powder as it actually needs, users save material and money. At the same time, the sustainable use of materials such as cobalt-chromium is beneficial to the environment. Excess powder can simply be reused after the printing process. 3D printers can ideally develop complex geometries such as corners and edges within the smallest amount of space. This means that dental technicians can increase the quality of their manufactured parts significantly.
Thanks to open interfaces, the 3D printer can be ideally integrated in the existing CAD/CAM process chains. The result is that dental laboratories do not have to convert their entire system. The advantages of this hybrid workflow: shorter production times, lower costs.
3D dental printing in metal - questions and answers
Hybrid workflow

Linking up with the milling machine is an important milestone on the journey to automated series production in dental technology .