The laser metal fusion process starts with the virtual 3D model of the component. During data preparation, the design data is converted into a build job file that can be read by the machine. The components are positioned on the substrate plate and, if required, support structures are attached. For the printing process, the components are broken down into individual layers (slices) and the corresponding laser paths are defined (hatching). The workpiece is finally built up layer-by-layer in the process chamber under shielding gas on a substrate plate. In the chamber, the supply cylinder, build cylinder, and overflow cylinder are next to one another in one axis. The recoater shifts the powder from the supply cylinder to the build cylinder (1). The laser then melts the first layer of powder according to the part contour in a way that is firmly bonded with the layer below (2). In the next step, the build cylinder is lowered by one layer (3). The component is, in a manner of speaking, constructed in the powder bed. The excess powder lands in the overflow cylinder. This process is repeated until the component has been generated completely. In order to increase productivity, TRUMPF uses multiple lasers that work simultaneously in its systems. This is referred to as a multilaser principle. Metal powder is finally removed from the finished part in an unpacking station. The component is then separated from the plate, the support structures, if present, are removed, and, if required, the workpiece is reworked.

Laser metal fusion – benefits, working principles, and applications of the additive technology
Laser metal fusion (LMF) is an additive manufacturing method where a workpiece is built up gradually in a powder bed. To do so, a laser melts down the metal powder in material layers precisely at the points specified by the component's CAD construction data. The process is therefore often known as metal 3D printing/3D metal printing; the terms laser sintering and laser metal fusion are also common in the industry. The process is optimally suited for series production of geometrically complex parts with delicate internal channels and cavities that cannot be produced using conventional processes such as turning or milling or can only be produced ineffectively. Components which exhibit high stability as well as a low weight are created using industrial 3D printing – this is particularly beneficial for lightweight design or customized implants and prostheses. Furthermore, laser metal fusion is a sustainable production method, as, compared to ablative processes, no chips (and therefore little excess material) are generated. With almost two decades of experience in additive technology, TRUMPF provides complete packages for powder bed processes that are mature for industry – consisting of machines, services, and digitalization from a single source. From part identification to the finished product and beyond – we cover the entire process chain for you.
Users can directly create functional components – e.g. flexible or rotatable structures – from 3D CAD models using LMF.
Using LMF, components with conformal cooling can be produced. They dissipate the heat right where it is created.
Additive manufacturing enables the construction of delicate structures in a complex arrangement.
Freedom in design: During 3D printing, the design determines the production of the component – unlike in conventional production processes.
Practically no setup time is required for 3D metal printing. Due to the multilaser option and the automation components, you can further increase the efficiency of your production.
The industrial part and powder handling from TRUMPF increases the productivity of your production.
A closed powder circuit ensures a clean and safe production environment.
The laser metal fusion process explained in brief
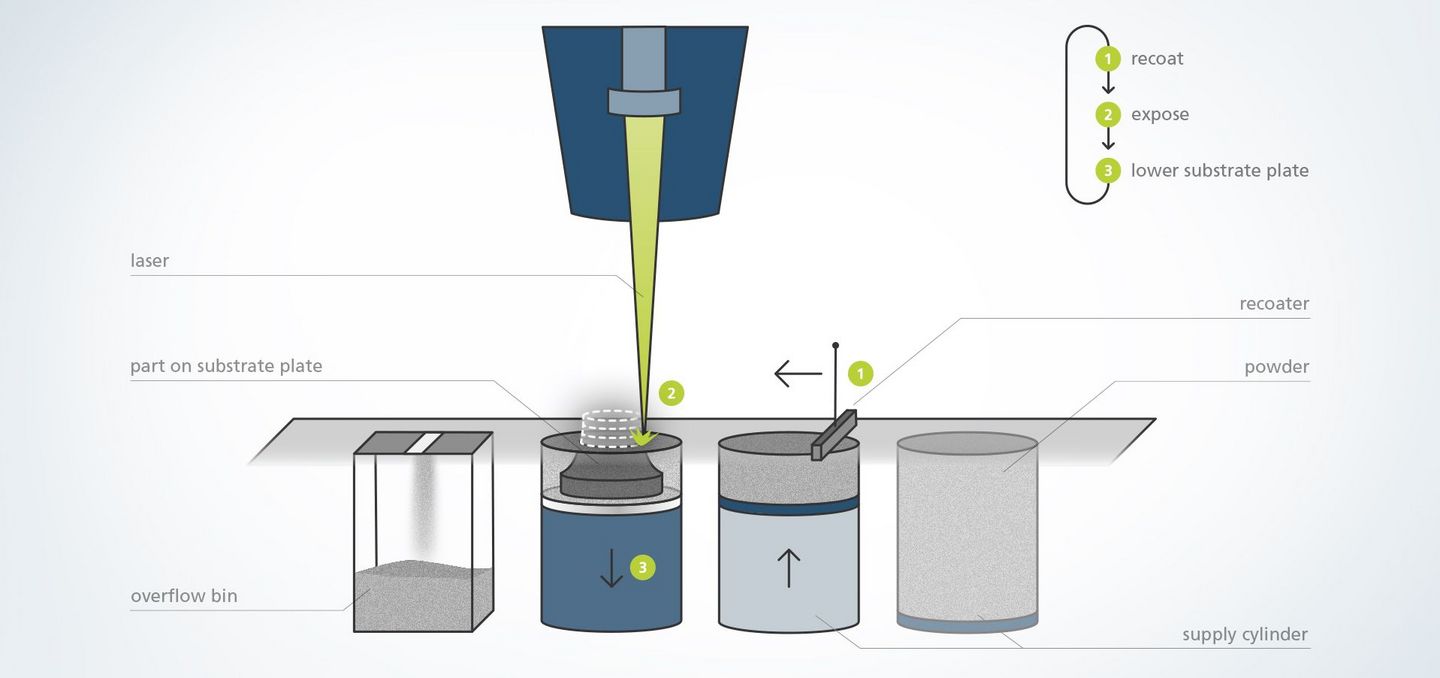
The operating principle of metal 3D printing explained in brief.