Paula snuggles up to her mum and listens spellbound to her bedtime story. She loves books, especially when someone reads to her. The five-year-old's ability to hear words and even music was something that seemed impossible shortly after her birth. Paula was born profoundly deaf. She couldn't hear the voices of her parents and siblings or the sounds of her environment. One in 1,000 children in Germany is born without hearing, like Paula. Their families are then faced with a decision. Do they choose hearing implants or sign language? Paula's parents were committed to providing their daughter with the most inclusive life possible, so they opted for a cochlear implant. A cochlear implant is a hearing aid that is implanted in the cochlea.
Complex system
These hearing systems consist of an audio processor with a microphone, and the implant itself. Patients wear the processor behind their ear. It detects sounds in the environment and adjusts the tones and volume, reduces distracting background noise and amplifies subtle sounds. Surgeons insert the implant under the skin. The cochlear implant assumes the role of sensory hair cells in the ear by electrically stimulating the auditory nerve, thereby restoring the ability to hear.
Removing barriers to hearing
The Austrian company MED-EL, based in Innsbruck, specializes in the development and manufacture of cochlear implants. Its product portfolio includes implantable and non-implantable hearing systems. The family business has 2,500 employees. In addition to clinics and medical professionals, audiologists are also among the customers who provide ongoing support to patients post-surgery.
Dietmar Köll, production manager at MED-EL, explains: "Not being able to see separates you from things - not being able to hear separates you from people." Köll and his team are working to change that. "With our products, we want to overcome hearing loss as a barrier to communication and quality of life and help people regain their zest for life. It is a lovely job."
No two ears are the same
MED-EL focuses on a wide range of products, because people's ears - or cochleas - are as unique as the individuals themselves. Dietmar Köll explains: "We adopt an extremely dynamic approach to our work and try to incorporate customer feedback into our products. That is why we offer a very broad portfolio with a modular structure. We have a range of processors and implants. We assemble these products based on the individual requirements of the patients. This allows us to find the optimal solution for different hearing situations."
Precise markings in tight spaces
Producing small batches with customized markings is a routine task at the Innsbruck production facility. This is where MED-EL assembles the cochlear implants and audio processors and applies markings to the small metal and plastic components. The Tyrolean hearing experts are currently focusing on two particular trends: To make the devices more comfortable to wear, the components are becoming ever smaller, while at the same time the requirements for traceability and documentation of products and manufacturing processes are increasing. The production team therefore has to apply more and more markings in ever-tighter spaces. The markings also have to be legible and durable. This requires dependable production technologies with stringent standards.
High-contrast and resistant
MED-EL uses three TruMark Station 5000 machines from TRUMPF to do the job. Equipped with lasers from the TruMark Series 3000, they mark components made of titanium, platinum-iridium and plastic. Deputy production manager Christoph Fankhauser explains: "We mainly apply serial numbers and unique device ID codes, or UDI for short, to metal and plastic parts. This machine-readable, universal product code is mandatory for medical devices in Europe. We also label the parts with symbols such as arrows and instructions to make handling easier for users." Uniform gradients are of utmost importance for MED-EL, as many of the labels are prominently displayed on the final product. A high contrast is crucial for this because it ensures good readability. "And, of course, the markings must be reproducible. In other words, the result must always be the same, even if there are possible fluctuations in material quality," emphasizes Fankhauser. "This requires a high level of power stability. The TruMark laser meets these requirements - even on the tiniest components."
A full sensory experience
Paula is unaware of all the dedication and hard work put in by the cochlear experts. For Paula, the joy of running around the house loudly with her siblings and attending kindergarten every day is simply part and parcel of her daily routine. Her cochlear implant has brought sound to life for her, and she now relishes it with all her senses.
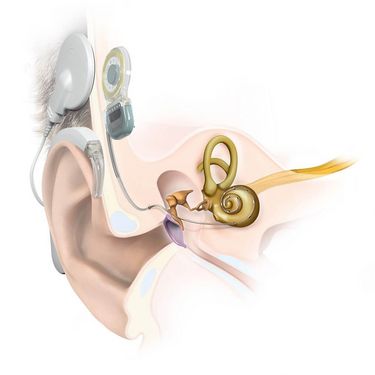
A cochlear implant consists of two parts: An audio processor with a microphone, which is worn behind the ear and detects sounds and noises, and the implant itself, which is inserted under the skin. An electrode array runs from the implant into the inner ear. This long, flexible platinum wire is fitted with electrodes and coated with silicone. When the audio processor receives sounds, they are transmitted to the implant as electrical signals. It converts these into electrical impulses, which the electrode array conducts into the cochlea to stimulate the auditory nerve. This transmits the auditory sensations to the brain, which interprets them as sounds and noises. Even those who are profoundly hearing impaired or born deaf can learn to hear with the device. The artificial impulse generated by the implant sounds different from natural sounds. Much like a new language, the brain must first learn to understand it. Regular language training helps with this.
© MED-EL