TruHeat VCSEL heating modules as an innovative step forward in battery manufacturing // VCSEL technology enables ecologically sustainable, higher quality and cost-effective battery production // Demonstration of TruHeat VCSEL heating modules for e-mobility // Presentation of the results of an experimental study
Battery Show Europe: TRUMPF TruHeat VCSEL drying solutions for advanced, cost-effective electrode manufacturing
Ulm/Stuttgart, 17 June 2024 – TRUMPF Photonic Components, a global leader in VCSEL solutions for industrial laser heat treatment, is showcasing its latest TruHeat VCSEL product developments for e-mobility applications at the Battery Show Europe in Stuttgart, Germany. Furthermore, the results of an experimental study with the research institute Production Engineering of E-Mobility Components (PEM) of RWTH Aachen University will be published in a whitepaper, which will be released at the Battery Show. It has been confirmed that the VCSEL-based laser heating systems can reduce the operational expenditures (OpEX) by up to 40 % and decrease the CO2 footprint by up to 40 %. Other advantages are the reduction of the equipment footprint by up to 50 % with the same electrode and cell quality.
More benefits of the TRUMPF TruHeat VCSEL heating system
The lithium-ion battery costs make up nearly one third of the total costs of battery-electric vehicles. The drying of electrode coatings is a delicate process and consumes most of the energy in Li-ion battery manufacturing. “Laser drying offers many advantages like improved energy efficiency, reduced floor-space requirements, and increased process control.” said Ralph Gudde, Vice President of Marketing and Sales at TRUMPF Photonic Components. ”Therefore, TRUMPF developed the TruHeat VCSEL laser heating systems to enable the homogeneous drying of very large surfaces with relatively low power densities.” he explained. TruHeat VCSEL laser heating systems are based on the latest generation multi-junction VCSEL arrays, and the heating system is optimized for thermal design with highly efficient driver electronics. The wavelength of 980nm is strongly absorbed by all battery electrode materials and therefore supports the high drying efficiency.
The TruHeat VCSEL laser heating systems have a modular design with separate zones. This enables the precise control of individual illumination zones to support not only optimal homogeneity but also the customization of intensity profiles, for example, a lower or higher intensity at the edges of the coating. Another unique property of the TruHeat VCSEL modules is their compactness and the low working distance. This enables easy integration, even in existing lines.
Visit TRUMPF at Battery Show 2024, Booth 833, see our live showcase and get your printed white paper
Digital images in printable resolution are available to accompany this press release. They must only be used for editorial purposes. Usage is free of charge if the source is cited as follows: "Photo: TRUMPF". Changes to the graphics – with the exception of cropping of the main motif – are not permitted. Additional photos are available in the TRUMPF Media Pool.
Contact person
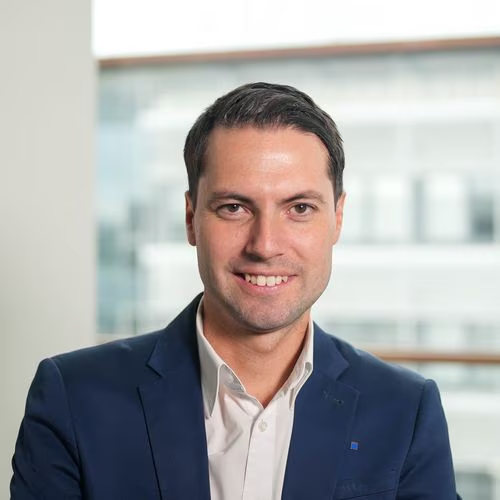