Order preparation processes are integrated in Oseon. Interfaces enable communication with adjacent sections , e.g., programming. You can use the production planning tool to simplify production planning. It provides reliable information on delivery dates, taking into account workstation capacities and the current status of production. Digitally connected with all production employees.
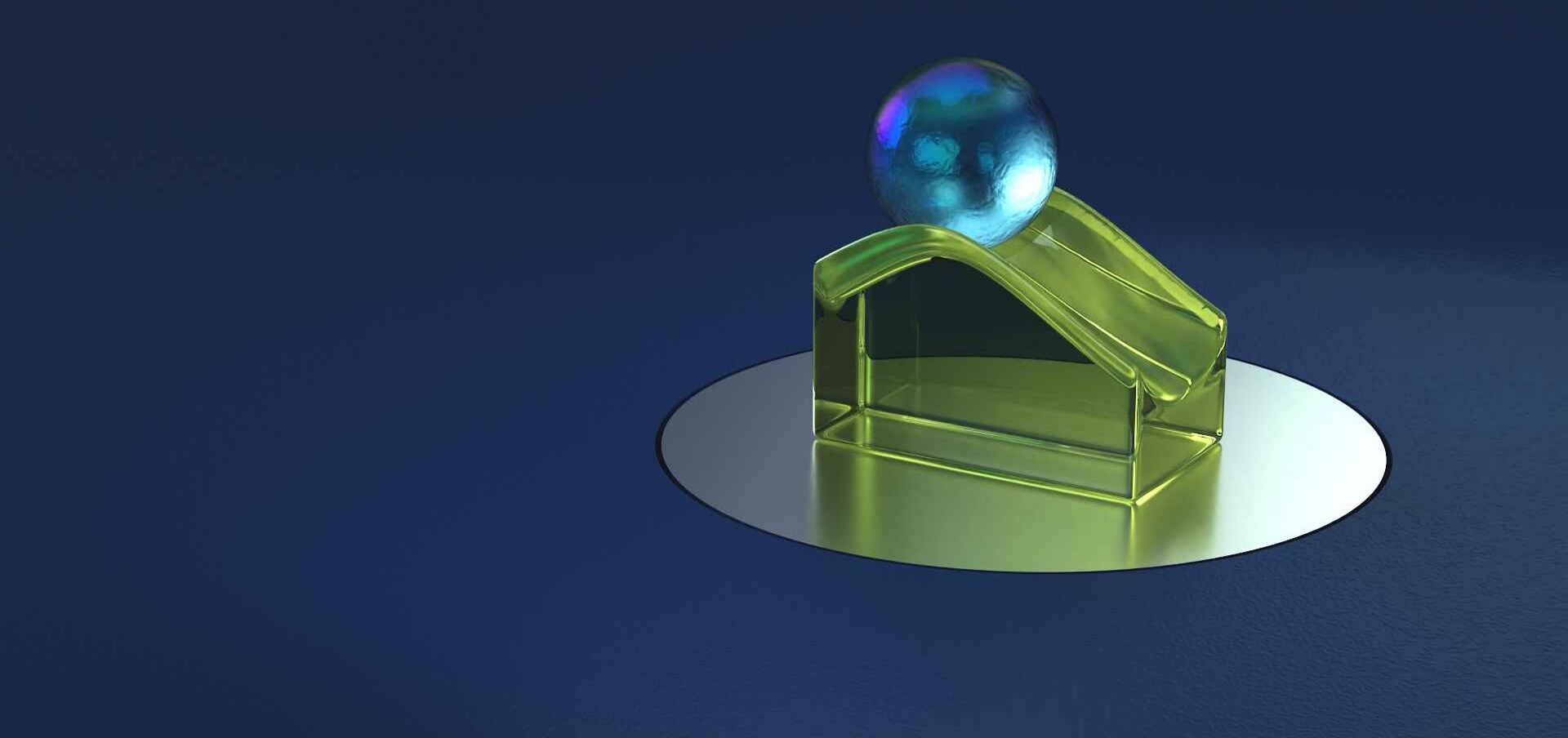
Production control: a perfect production flow with Oseon
As a sheet metal processor, how do you keep an overview over your processes? With Oseon – a comprehensive solution for production and material flow control, which supports users according to their roles and displays your processes consistently and transparently. This opens up growth and savings potential for you.
Oseon: Work flows
Information is generated at many points in your production. The Oseon software ensures that you receive all relevant information at the correct time and at the correct location, specific to the particular users. To this end, Oseon combines the production control of the sheet metal process chain with the benefits of a logistics system. Standard interfaces ensure simple integration of your existing facilities, automation and systems. The result is a seamless flow of information along the entire production chain. To put it simply: work flows
Oseon Go digitalises all core processes in your production.
Oseon Grow is an extension of Go in the areas of storage, logistics and interfaces.
You achieve a complete network with Oseon Flow.
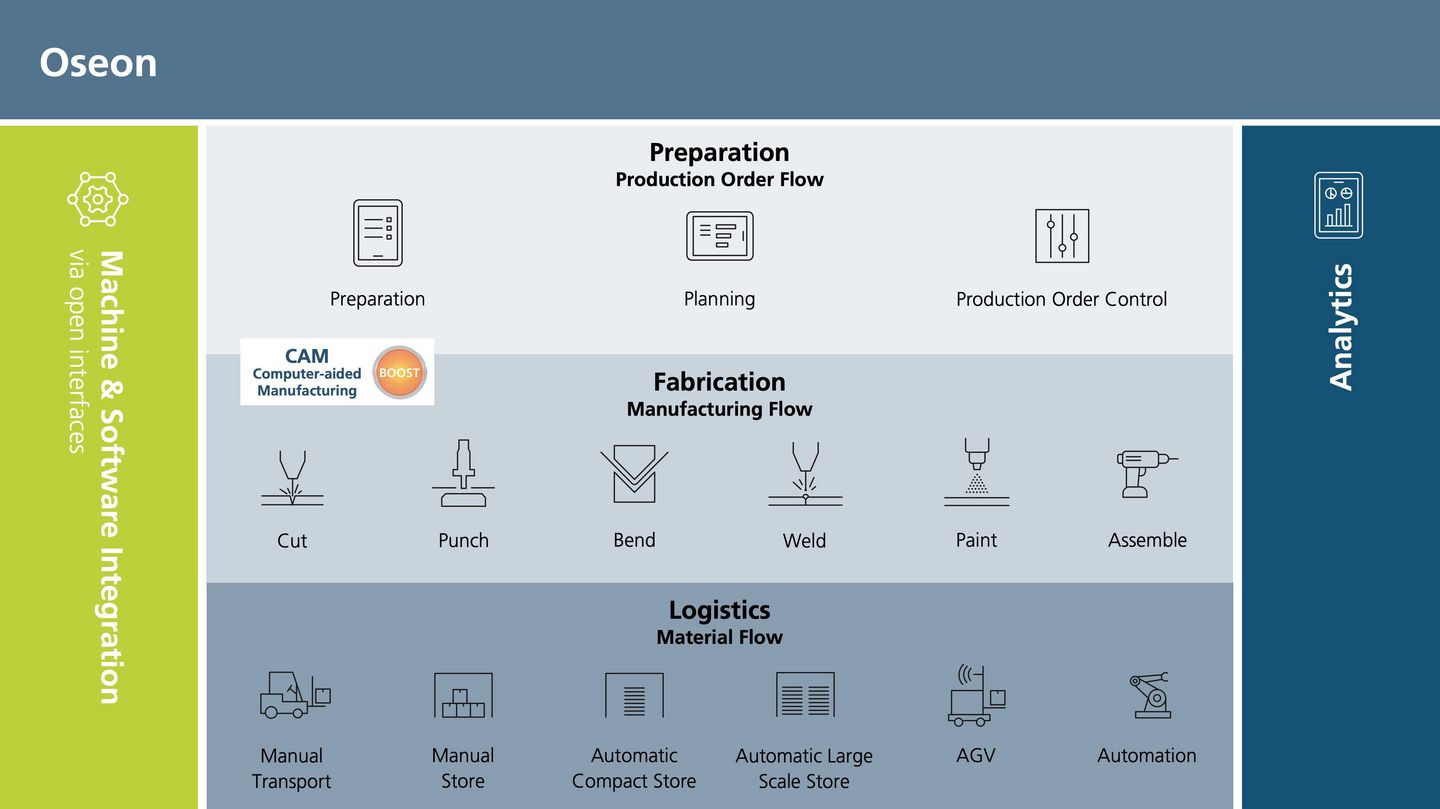