The right tricks allow you to design your parts more cost-effectively. The solution: reducing the number of single parts and process steps. The support bracket shown here originally consisted of three parts connected with four weld seams, plus separately cut threads. It was redesigned out of just one bending part – without welding. An additional bend even allows you to reduce the sheet thickness and form the threads directly on the punching machine.
Part optimisation
What potential is hidden within your parts? Find out in our workshops and seminars on part design. If you want to manufacture parts more profitably, produce new parts or enter new types of technology – the relevant specialist knowledge will help you trim your parts for success, while also saving money. Because cost-efficiently designed parts are the key to efficient manufacturing, require fewer process steps and reworking, and pave the way to networked production.
Keep materials, processing steps and costs to a minimum by designing your parts according to their function.
Part optimisation exercises on over 700 sample parts and your own components to ensure cost-effective part design.
Learn design rules for creative ideas and new solutions and train your eye to evaluate feasibility and economic efficiency.
Experience the application, design and manufacturing possibilities of sheet metal and tubes in over 1,000 training courses.
Sheet metal part design
Lighter, cheaper, or more functional: How would you like your parts? When sheet metal parts have a well-thought-out design, this allows your machines for laser cutting, punching, or bending to reach their full potential – while saving on materials, costs and effort.
Example: optimised axis stop
The axis stop is conventionally produced out of a welded construction with a semi-finished product and milled parts. The many work steps are both time-consuming and cost-intensive. The new design made of two sheet parts reduces the number of parts and thus the joining processes and material usage.
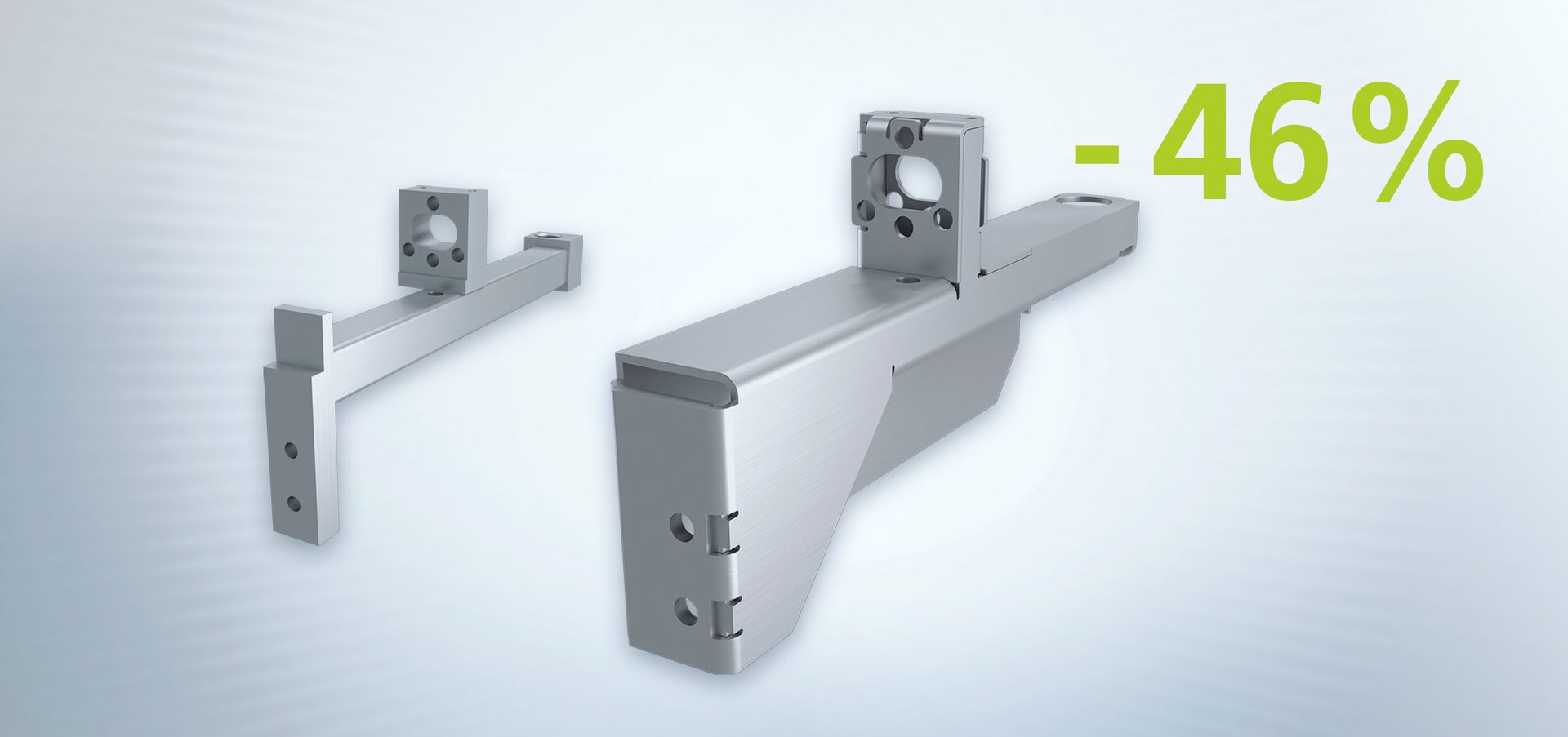
1. Sawing
...all components to size.
2. Milling
... the contact surfaces, oblong holes and stepping.
3. Drilling
... all holes in the components.
4. Welding
... all four components.
5. Laser cutting
... allows for any desired geometries to be cut into sheet metal, and creates bores.
6. Tapping
... for more strength compared to cut threads.
7. Bending
... replaces welding and decreases the number of parts.
8. -46% in costs
... with the new design