Tubes and profiles allow you to give shape to visions: For example, in vehicle frames, in furniture and lamps, in mechanical and plant engineering. A fully automated tube processing chain helps you to counter skills shortages and save money, and to tap into new business areas. TRUMPF provides all-encompassing solutions to fulfil your every requirement. When do you opt for unlimited possibilities from a single source?
The challenges of tube processing
What would be your ideal process chain for tube processing?
Increased security through seamless support along the entire process chain
The process chain for tube processing consists of storage, processing and welding. It can be automated precisely to suit your requirements. When fully automated, the process chain comprises up to 7 steps: storage, loading, laser tube cutting, unloading and sorting, tube bending, 3D laser cutting and welding. Our software and service solutions simplify the process. Alternatively, you can partially automate the process steps. The choice is yours – work with us to design the perfect process chain for your needs.
Overview of the process steps
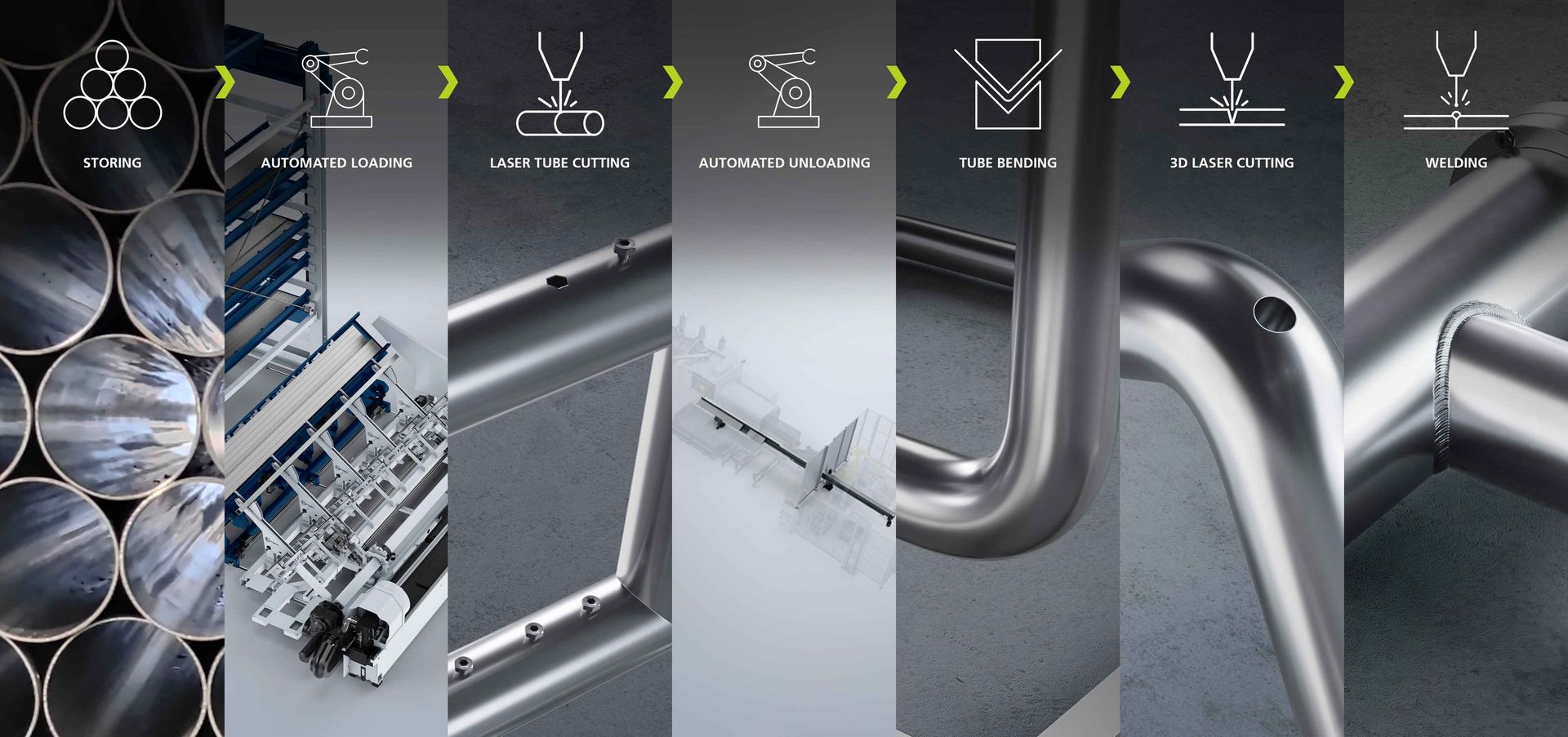
1. Storage
The right storage solution for your raw materials and more storage space. The STOPA store and our Oseon production control system allow you to structure your warehouse and reduce search times.
Find out more2. Automated loading
Load your laser tube-cutting machine fully automatically: the machine requests raw material via an interface and is loaded directly from the storage cassette.
Find out more3. Laser tube cutting
Customize complex contours and innovative tube designs with an economical, efficient and flexible technology that avoids rework and errors.
Find out more4. Automated unloading and sorting
Unload and sort automatically via the unloading automation interface with longitudinal conveyor belt. This reduces operator involvement as well as cutting out errors and saving money.
Find out more5. Tube bending
Highly efficient and precise CNC tube bending technology reduces component costs and avoids the need for welding and soldering work. We place our trust in transfluid® as a partner for this work.
Find out more6. 3D laser cutting
A TruLaser Cell system allows you to create complex geometries in bent tubes, both in bending zones and for final trimming.
Find out more7. Welding
Automated arc welding allows you to join components productively and with process reliability. Automated laser welding also saves you time and money.
Find out moreModules for your fully automated production solution for tube processing
We provide the ideal components for each process step from a single source, either fully automated or a combination of automated and manual components. In other words, your solution can range from a single stand-alone machine to a fully automated system – fully customized to suit your requirements. You also have access to the right software and services.
Master new challenges
The benefits of a fully automated production solution for tube processing
When using automated processes, you need fewer qualified specialists.
Reduce the risk of errors and increase productivity and efficiency using automated processes.
Reduce cost pressure with strategic purchasing and shorter throughput times.
Counter a lack of space with vertical storage and optimised space utilization.