With electronic and electrical engineering products, spatter during the welding process can result in short circuits or pores in the welding seam. The TruDisk Pulse reduces these risks with its optimal input coupling rate. The material is heated evenly, which results in a more stable weld pool. As a result, there is less spatter. This will help you avoid excessive rejects and cleaning cycles for the system.
Green light for copper welding
The pulsed high-power laser TruDisk Pulse allows you to efficiently weld highly reflective materials such as copper. The optimal absorption, as well as the high peak pulse power of 4kW with pulse durations in the milliseconds range, enables unparalleled application results when welding points and short seams. The laser is therefore predestined for use in electrical engineering and electronics. The TruDisk Pulse is based on the proven disk laser technology.
Many highly reflective materials, in particular copper, absorb green laser light much better than infrared light.
Prevent spatter through more uniform heating and a more stable weld pool.
The more stable welding process results in more consistent weld point diameters and uniform welding depths.
The application results are largely achieved irrespective of variations in the material batch.

Consistent spot welding
Spot welding with the TruDisk Pulse provides especially low-spatter and reproducible results. The diameter and depth of the points remain consistent throughout the process.

Direct copper bonding (DCB)
The TruDisk Pulse can also weld thin materials with no impact on the base. For example, copper tracks can be contacted onto substrates using ribbons or wires, without damaging the underlying ceramic.

Various surfaces
Whatever the surface quality, the TruDisk Pulse welds copper seams with consistent quality as a result of the more stable process at a wavelength of 515 nm, and ensures that you will have highly robust production. Most of the time-consuming preparations for standardised preparation of the surface finish using sandblasting, tin plating or similar methods are omitted here.

Laser-welded electrical contacts
With the TruDisk Pulse, you can reliably weld sensitive electronic components by yourself. With the green wavelength, you can reduce spatter by over 95% in comparison to infrared light. This means that you effectively avoid short circuits and the resulting faulty components.
TruDisk Pulse 221
|
TruDisk Pulse 421
|
|
---|---|---|
Laser parameters | ||
Laser power | 200 W 1 | 400 W 1 |
Maximum peak pulse power with LLK length 10 m | 2 kW | 4 kW |
Maximum pulse energy with LLK length 10 m | 20 J | 40 J |
Maximum gating ratio | 10 % | 10 % |
Adjustable pulse duration | 0.3 ms - 50 ms | 0.3 ms - 50 ms |
Beam quality at the input coupling in the LLK | 4 mm▪mrad | 4 mm▪mrad |
Numerical aperture at the output coupling after LLK | 0.1 | 0.1 |
Wavelength | 515 nm | 515 nm |
Minimum laser light cable diameter | 100 μm | 100 μm |
Structural design | ||
Width | 1340 mm | 1340 mm |
Height | 1430 mm | 1430 mm |
Depth | 725 mm | 725 mm |
Maximum number of laser light cables | 2 | 2 |
Installation | ||
Protection class | IP54 | IP54 |
Ambient temperature | 10 °C - 50 °C | 10 °C - 50 °C |
The technical data of all product versions as a download.

TruControl
TruControl is the quick and easy-to-use control for TRUMPF solid-state lasers. It regulates the laser power in real time in order to deliver reproducible results. Additional modules are specially tailored to the requirements of the TruFiber. For example, the CutAssist option automatically adapts the laser parameters to the speed of the guidance system. In order to ensure that parts are traceable, the DataStore module records all quality-related data.
If external control systems are present, TruControl will communicate with them via all standard interfaces. Inputs are made via the touchscreen of the operating panel or via a panel PC. You can integrate your laser into the network via Ethernet and connect multiple PCs.
With TRUMPF you have the option to flexibly adapt your solid-state laser to your installation and operating situation. This applies, for example, to all beam guidance components and the control. Interfaces for different optics are provided right from the start. To save costs, your beam source can also supply several work stations at the same time. The TRUMPF Remote Service helps you to ensure your systems remain available, anywhere and at any time.

There are many different options for the beam guidance that will enable you to plan flexibly with your laser. The plug & play optical laser cables can be easily connected to different work stations. Here, you choose the number of fibre outlets up to a total of two. The laser power can be flexibly divided across the outlets. This allows multiple work stations to operate simultaneously with split laser power or one after the other with full laser power. The modular design means that the laser power and the number of outlets can be changed retrospectively in the field at any time.

With the laser network, you can connect one or more lasers with up to two work stations in each case. In the process, your laser either splits its power to multiple stations, or it supplies them by taking turns with full power. This will enable you to combine different applications such as welding or cutting with one another.

In the event of a fault, TRUMPF service experts will remotely access your laser via a secure remote connection. In many cases the fault can be remedied directly in this way, or the configuration of the laser can be modified in a way that permits you to continue manufacturing until the spare part arrives. This enables maximum availability for you.
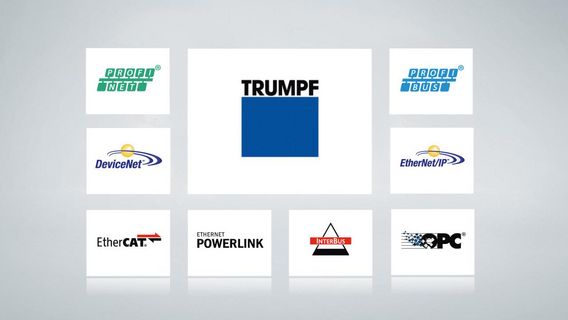
Interfaces are key for the integration of a TruDisk Pulse laser in your machine or production line. The solid-state lasers from TRUMPF offer interfaces to all common fieldbus systems. Also available: real-time interface, parallel digital I/O, interface for process sensor systems, OPC UA software interface, analogue input board, interface for intelligent TRUMPF optics.

Intelligent optics can be synchronised with your laser via a dedicated interface. This will allow you, for example, to use the PFO scanner optics optimally for your purposes. You can program the processing optics easily using the laser control. You do not need any additional PCs or control systems.

Processing optics and optical laser cables can be cooled easily and conveniently using the laser cooling water. Separate cooling is therefore not necessary.
The WeldAssist database provides you with welding parameters for various materials and focal diameters. The simplifies the set up of frequently changing laser applications.
Thanks to the TRUMPF sensor system, your production will always be both effective and cost-effective. The sensor products VisionLine, CalibrationLine or integrated pyrometers ensure stable processes by monitoring all the procedures in laser production, thus making a key contribution to your process reliability. Processing continues uninterrupted during the measurement – no interruptions are required, saving you valuable production time.
Image processing
TRUMPF VisionLine image processing detects features on the components and ensures that welding is always performed in the correct location.
Calibration tool
The TRUMPF CalibrationLine tool checks and corrects the focal position and laser power on the workpiece at regular, individually definable intervals.
Lasers and laser systems – with us, the perfect pair. All beam sources are optimally attuned to the requirements of the TRUMPF laser systems. You can choose between numerous variants and options, resulting in a system that is precisely tailored to your task. It is, of course, also possible to integrate our lasers directly into your production lines.
TRUMPF offers you all the components you need for beam guidance from the laser to the workpiece. This also applies for various focusing optics which have proven themselves to be precise and reliable over many years of industrial use. The optics can be easily integrated – both in stand-alone processing stations as well as in complete production lines. The modular structure enables the optics to be continually adapted to the laser types as well as the different processing situations.
Focusing optics
Whether for welding, cutting, ablating, heating up or drilling: with robust focusing optics from TRUMPF you can attain high-quality process results.
Programmable focusing optics
The ideal optics for remote processing
This product range and information may vary depending on the country. Subject to changes to technology, equipment, price and range of accessories. Please get in touch with your local contact person to find out whether the product is available in your country.
Footnotes-
The laser power at the workpiece may deviate from the rated power depending on the optics configuration.