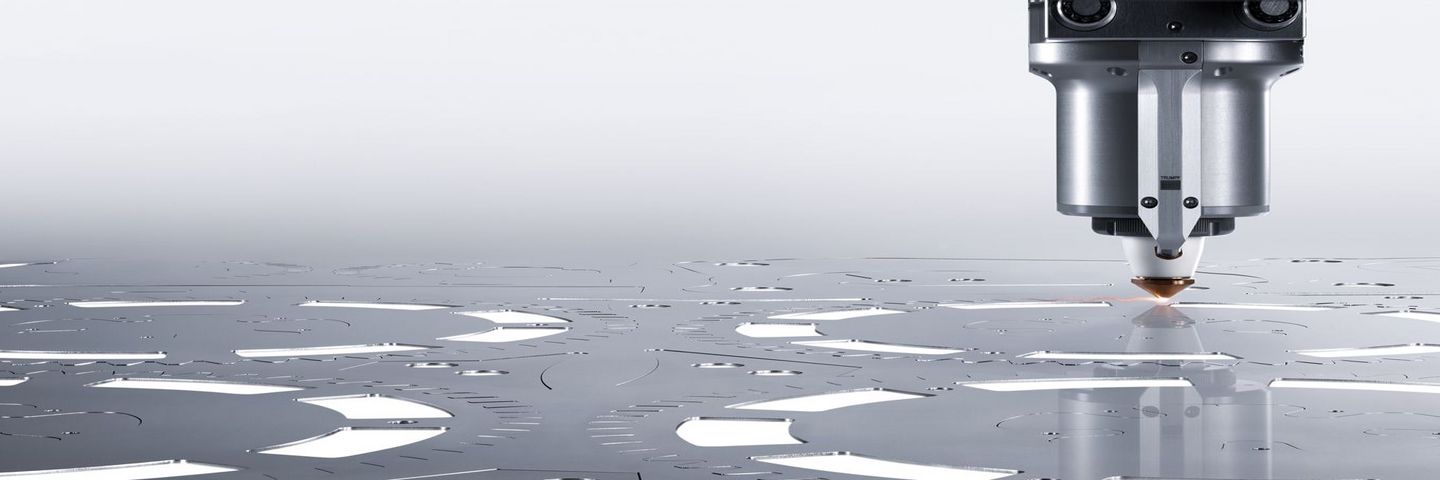
Our portfolio contains the right machine to meet any requirement, regardless of the type of sheet metal you need to process. We provide targeted advice when choosing between CO2 and solid-state lasers and will be glad to find the best, most cost-effective solution for you. Your application is the key factor determining which machine is the right one for you. However, we don't just focus on cutting times: we also strive to optimize upstream and downstream laser cutting processes. We are your one-stop supplier in this regard: providing the machine, laser, automation, software and the certainty of having an extensive international service network.
An overview of the advantages our laser cutting systems give you.
The possibilities are almost unlimited: use the wide range of smart functions from TRUMPF to fully utilize your machine's laser power. How? Find out here.